The rate of chemical reactions depends on a number of factors, including the temperature or the concentration of the reactants. As it turns out, a small addition of a foreign substance can affect the kinetics of the reaction and thus speed it up considerably. This issue is the subject of catalysis. It is now of great importance, especially in the chemical industry. Many large-scale technological processes would be impossible without catalysts. Moreover, enzymes, which catalyse biochemical processes, play a key role in the life processes on Earth.
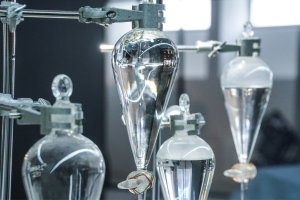
Catalysis – what is it and how is it classified?
Catalysis is defined as a phenomenon of increasing the rate of a chemical reaction by using a substance that is neither a substrate nor a product of that transformation. Such a substance is called a catalyst.
Basic types of catalysis are as follows:
- Homogeneous catalysis – in this type of catalysis both the substrates and the catalyst are in the same physical state. Most often, it is a liquid or gaseous phase. In this case, the catalyst reacts with one of the substrates, forming an unstable intermediate complex, which in turn reacts with the other reactant. As a result, reaction products are formed, and the catalyst is recovered. It should be noted that not all reactions proceed this way. In fact, multi-stage processes are the most common kind. An example of a homogeneous (or single-phase) reaction is the oxidation of sulphur (IV) oxide to sulphur (VI) oxide. All components, i.e. substrates, the catalyst and products, are present in the gas phase.
- Heterogeneous catalysis – this is the most commonly used type of catalysis, e.g. in chemical industry processes. Here, the catalyst is in a different physical state of matter than the other reactants. It is usually a solid, or so-called ‘contact’. The substrates adsorb on its surface. Then, the catalyst reacts with them. The resulting products desorb and leave the contact surface, making room for the next substrates. The use of this type of catalysis makes it possible to carry out, for example, reactions between gaseous substances that do not normally react with each other. Given that heterogeneous catalysis is very important from an industrial point of view, one of the main issues of catalysis is the development of catalysts made of different materials and having shapes that provide the largest possible contact surface.
- Enzyme catalysis – enzymes are, besides ferments, a group of proteins that are involved in the biocatalysis of biosynthesis and decomposition reactions. These processes take place in the cells of living organisms and bodily fluids. Enzymes, just like ‘classic’ catalysts, lower the activation energy of a biological reaction. On their surface, they have the so-called active centres. Due to their shape and structure, these centres are compatible only with specific substrates. Hence, the selectivity of enzymes as catalysts is 100%. Furthermore, such catalysis is referred to as the key and lock model. After the formation of the enzyme-substrate complex, some of the bonds are loosened and the products are formed. The enzyme is then released and returns to its original form.
Autocatalysis is an interesting phenomenon. It occurs when the resulting product of a reaction becomes its catalyst. Hence, with time, the reaction proceeds faster and faster. An example of an autocatalytic process is the reaction of KMnO4 with hydrogen peroxide in an acidic environment. The ions that are formed (i.e. Mn2+) act as a catalyst for the original reaction.
Catalysts
Catalysts are chemical substances that, when introduced into a reaction system, accelerate the chemical reaction. What is important, they do not undergo chemical transformations during the reaction, and they are recovered in their original form once the reaction is complete. The catalyst added to the reaction system forms an unstable transient bond with the substrate. This allows the activation energy to be lowered. What is important, the catalyst is not included in the stoichiometric equation of the overall process. Moreover, even with a catalyst, it is not possible to initiate a reaction that is not thermodynamically feasible.
In order for a given chemical reaction to occur under certain conditions, it is necessary to provide energy greater than the required activation energy. In this case, the role of the catalyst is to reduce the amount of energy required, so that the reaction can start more quickly. It is worth remembering that the catalyst does not affect the shift in the equilibrium state. It merely accelerates the moment of its achievement. The faster it does this, the more active it is considered to be. Thus, catalyst activity is defined as the difference in the rate at which the reaction reaches equilibrium in the presence and absence of the catalyst. Another criterion characterising catalysts is their selectivity. It is defined as the ratio of the amount of product formed to the total amount of all products formed during the reaction. Substances used as catalysts in industrial processes usually achieve selectivity of 70% to 90%. In this respect, enzymes are unique. The level of selectivity they achieve in biochemical reactions reaches up to 100%.
The importance of catalysis in industrial processes
Currently, catalysis plays a key role in many processes, especially in the chemical industry. Catalysts contribute to more efficient production of chemicals, which in turn are used, for example, in the production of fertilisers. Three examples of chemical industry processes that rely on catalysis are presented below. These catalysts are among the most commonly used. However, one should remember that new or modified solutions are constantly being introduced onto the market, and they are succeeding in gradually replacing previously used substances.
Nitric (V) acid production
The production of nitric (V) acid consists of several successive stages. First, is the combustion of ammonia in oxygen to nitric (II) oxide and water. To increase the process efficiency, it is carried out using a catalyst, which is an alloy of platinum and rhodium (93% Pt and 7% Rh). This alloy is used to produce wires from which special meshes are woven. Two or three meshes are placed in the reactor, perpendicularly to the flow of the reacting gases. However, this method has some limitations. The moving gases cause friction against the meshes, resulting in their degradation and loss of platinum. These losses are particularly noticeable in the oxidation section, where there is increased pressure and high temperature. In addition, platinum meshes are relatively sensitive to poisoning caused by insufficient purification of reacting gases from interfering substances, e.g. sulphur. During the catalytic oxidation of ammonia, nitrous oxide is formed as a by-product. Currently, the solutions reducing its emissions are available on the market. For this purpose, an oxide catalyst based on aluminates is used near the Pt-Rh alloy meshes for high-temperature decomposition of nitrous oxide in nitrous gases. A characteristic feature of this catalyst is its high selectivity of decomposition in relation to N2O.
Oxidation of SO2 to SO3
One of the most important steps in the industrial production of sulphuric (VI) acid is the oxidation of sulphur (IV) oxide to sulphur (VI) oxide. This process is performed using the contact method. Many substances can act as a catalyst in this oxidation reaction. They accelerate the reactions to varying degrees. It has been experimentally proven that the highest efficiency is achieved using vanadium catalysts. They consist of vanadium (V) oxide, which is deposited on a support (usually silica). In addition, it also contains activators (sodium oxide or potassium oxide) and other additives that affect, among other things, its strength at high temperatures. The amount of vanadium (V) oxide in the catalyst ranges from 5 to 7 wt%. It achieves its greatest efficiency at relatively high temperatures. On its surface, the vanadium catalyst has active sites where the O2 and SO2 molecules are adsorbed. There, their reactions take place, followed by desorption of the resulting products. Insufficient purity of the substrates fed into the reactor can result in catalyst poisoning, i.e. the deactivation of its active sites. In this case, the poisons include chlorine, fluorine and arsenic.
Ammonia production
Another catalytic process in the chemical industry is the synthesis of ammonia. The process itself is so slow that it is necessary to use appropriate contacts. In this case, the most favourable catalyst is iron activated with a small amount of alumina and potassium oxide. It is formed by burning iron in the presence of oxygen and then melting the resulting Fe3O4 with Al2O3 and K2O. The alloy (most often) in the form of granules is a finished catalyst. As in other processes, during the ammonia synthesis process the iron catalyst causes the absorption of hydrogen and nitrogen at its active sites and the desorption of the resulting products. Compounds responsible for the degradation of the iron contact are mainly sulphur, carbon dioxide and water vapour.