As time passes, we can observe the growth of fuel consumption. Unfortunately, the distillation of fractional crude oil does not ensure an adequately high amount of fuel, so it cannot be the only source covering the demand. In consequence, various methods of fuel production have been developed, the most important being the processing of hard coal or synthesis gas and what is known as ‘cracking’ from higher fractions of distillation of fractional crude oil.
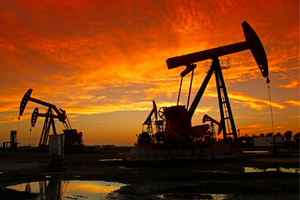
What is cracking?
Cracking refers to a number of technological processes where the treatment of heavy fractions of crude oil and petrol gives a result having the form of petrol and oils. The term ‘cracking’ is the activity of initiating a controlled decomposition of long aliphatic hydrocarbons which exist in heavy fractions, for example in mazut and in the oil fraction formed as a result of crude oil refining. Such a reaction produces compounds whose structure consists of shorter carbon chains. Such molecules are present in such substances as petrol or diesel oil and are a mixture of alkanes and alkenes with shorter chains.
The chemism of cracking
To make it simple, the processes that occur in cracking are based on the breaking of single chemical bonds existing between the atoms of the element (carbon). During the changes, free radicals are formed. The reaction may be induced in two different ways: with the use of heat (thermal reaction) or in the presence of catalysts (catalytic reaction). There is also a more elaborate, less commonly used method , that employs ionising radiation (radiational reaction). The processes that occur during cracking include a number of changes such as the isomerisation of hydrocarbons, dehydrogenation to aromatic hydrocarbons, and their condensation to polycyclic aromatic hydrocarbons.
Thermal cracking
In the refining and petrochemical industry, which uses thermal and thermocatalytic processes, a great role is played by the reactions of dissociation and formation of homoatomic C-C bonds and heteroatomic C-H bonds. There are two possible mechanisms responsible for such reactions: the radical mechanism and the ionic mechanism. Normally, thermal cracking without a catalyst is predominated by the radical mechanism, which is also generated during the reaction of pyrolysis. Several variants of thermal cracking have been developed, depending on the process conditions. One of them is high-pressure cracking (2–7 MPa), which is carried out at a temperature of around 470–540 oC. In such conditions, the crude oil fraction decomposes from ligroin and mazout, and vehicle petrol is produced. Another type of process is light cracking, which includes the breaking of the distillation residue of crude oil, which eventuates in a substance known as ‘soft asphalt’. It is carried out at a slightly lower temperature (460–510 oC) and under a much lower pressure (approx. 0.5–2 MPa), which makes it possible to produce fuel oil. The third type of thermal cracking involves the use of an even lower pressure (0.1–0.3 MPa) but at high temperatures (430–550 oC). It has been empirically proven that it is possible to use such a reaction where petroleum coke is produced from soft asphalt. Sometimes referred to as process-retardant cracking, it provides the raw material required to produce high-crystalline needle coke, used in the production of electrodes for the steel and aluminium industries. That variant also has its by-products, such as gases and petrol as well as medium and heavy kerosene fractions. The last type of common thermal cracking is the pyrolysis, also called steam cracking. This term includes the process of decomposing liquid and gaseous kerosene-based raw materials such as low-octane petrols, gas oil, ethane, butane and propane in conditions being somewhat different than those specified above. Pyrolysis is performed in the highest thermal conditions, using temperatures ranging from 700 to 1200 oC, under normal pressure of around 0.1 MPa. The hydrocarbon input, being a raw material, is thinned with steam and heated in a furnace without oxygen, in a short time. An increased efficiency is possible if the period when the raw material remains in the furnace is reduced to milliseconds. Gas is quickly extinguished immediately on achieving the cracking temperature. Such conditions lead to the formation of a gas with a high content of unsaturated hydrocarbons, including the valuable ethylene as well as other raw materials desired in the petrochemical industry. In the event of using light hydrocarbons, lighter alkenes are produced such as ethylene or butadiene. The use of heavier hydrocarbons results in the formation of products with a high content of aromatic hydrocarbons and compounds that can be included in petrol or fuel oil. Another relation is the fact that a higher temperature supports the production of ethylene and benzene, while a lower temperature, the production of propylene, C4 hydrocarbons and liquid products. Presently thermal cracking is used in the industry mostly to improve the very heavy kerosene fractions or to produce light fractions/distillates, burner fuel or petroleum coke.
Catalytic cracking
As the name indicates, catalytic cracking is carried out in the presence of appropriate catalysts. The use of such additives makes it possible to reduce the required high temperature and pressure of cracking. The most common catalysts include hydrated aluminium silicates AlCl3 and Cr2O3, which contain appropriate activators such as nickel, cobalt or manganese oxides. In practice, they are industrially used along with 20% of zeolite. This depends on the applied processing method, specifically on the type of catalyst that can be mobile, fixed-bed or dusty. The conditions in which catalytic cracking is conducted are slightly lighter, as it is usually carried out at a normal or slightly increased pressure (0.1–0.2 MPa) and at a temperature of around 450–510 oC. The raw material in catalytic cracking normally includes light oil fractions that boil at 280 to 350 oC, and the products are the extremely desirable petrols with a high octane number as well as diesel oil. The speed of decomposition is higher with the use of a catalyst rather than with thermal cracking. If we compare the products of thermal and catalytic cracking, the use of catalysts allows for the formation of substances with a higher content of branched paraffins, cycloparaffins and aromatic hydrocarbons. In the conditions enabled by catalytic cracking, there also occur, at a high speed, such reactions as:
- Decomposition of homoatomic C-C bonds in paraffin molecules, which results in the production of low-molecular olefins.
- Dehydrogenation of naphthalenes with the production of aromatic hydrocarbons.
- Formation of olefins as a result of breaking naphthalene rings.
- A parallel polymerisation of olefins and their condensation with dienes, which is consequently reflected in the production of aromatic hydrocarbons.
An interesting variety of catalytic cracking is the hydrocracking, which uses the addition of gaseous hydrogen. Such an additive has many positive effects, which include:
- for raw materials containing high amounts of paraffins, preventing the formation of polycyclic aromatic compounds;
- reduced production of tar and contaminants;
- supporting a more efficient operation of the catalyst: prevents the accumulation of disturbing coke
- the possibility to acquire products with a lower content of sulphur and nitrogen;
- producing fuel with a high cetane number.
It should be noted that the conditions of catalytic cracking also include the demand of reforming processes such as isomerisation, cyclisation and aromatisation. In consequence, the products of such reactions are petrols with a higher octane number.
Sources:
https://encyklopedia.pwn.pl/haslo/kraking;3926970.html
https://www.naukowiec.org/wiedza/chemia/kraking-termiczny-i-katalityczny_1167.html
https://arquidiamantina.org/pl/kraking-chemia/