Fossils, which are non-renewable energy sources, are used as fossil fuels. These include coal, oil, natural gas and peat. Fossil fuels are substances of organic origin. Their basic constituents are elements such as carbon, hydrogen and sulphur. During combustion processes, they are oxidised, resulting in the formation of the corresponding oxides. The oxidation reaction also produces energy. A good quality fuel is considered to be one that burns intensively and with the release of large amounts of heat, which can be used efficiently. Fossil fuels are often not suitable for direct use and therefore need to be properly processed.
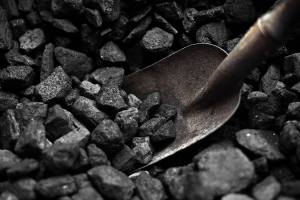
Hard coal
Hard coal is a sedimentary, combustible rock of organic origin. It is formed by the transformation of accumulated organic matter. This is accompanied by biological, biochemical, geological and geochemical processes, which are referred to by the term carbonisation. The matter is then enriched in elemental carbon. Hard coal typically contains between 75 and 92% C, while another variety of coal – anthracite – can contain up to 97%. These processes are extremely lengthy and occur under specific temperature and pressure conditions.
The processing of hard coal includes:
- Coking – is the most important process for the chemical processing of hard coal. As a result, coke is obtained. The coal is heated at a temperature of 900 to 1100 ᵒC, without access to air. Under these conditions, the fuel decomposes and coke (in the form of a solid residue) and a mixture of gases are produced, which are called light coking products. In the coking process, it is important to properly prepare the raw material for coking so that the final product is of good quality, i.e. has the right granulation, porosity and mechanical strength. The grade of hard coal is significant here. The coal preparation process involves weighing, grinding and mixing.
- Gasification – the essence of this process is the transformation of extracted coal into a gas with energetic properties. Hard coal gasification is carried out in industrial installations specially adapted for this purpose. The gasification process takes place in the presence of air or pure oxygen. Importantly, the hard coal – the raw material going into the reactor of the gasification plant – does not have to be of the highest quality. Contaminated coal is also well suited to this. However, the degree of purity of the raw material determines the quality of the product. Synthesis gas, which is produced by coal gasification, is an important substitute for natural gas in the chemical industry.
Read also: allotropic varieties of carbon.
Crude oil
Crude oil is a complex mixture of chemical compounds. Its composition (approximately 80-90%) is predominantly liquid hydrocarbons or dissolved solid hydrocarbons. Crude oil consists primarily of paraffinic, aromatic and cycloparaffinic hydrocarbons. In addition to the above, organic compounds containing elements such as oxygen, sulphur or nitrogen in their structures are also found in crude oil. Depending on where and where the oil is extracted, it varies in appearance and chemical composition. Its hydrocarbon composition and the presence of other components affect the choice and course of its processing.
Basic crude oil processing includes:
- Distillation – this process aims to separate the crude oil into individual fractions (hence the name fractional distillation), which can then be used independently or sent for further processing. Crude distillation plants consist of two single-stage distillation systems. The first is distillation under atmospheric pressure and the second is distillation under reduced pressure. Under atmospheric distillation, three main fractions are obtained: first distillation naphtha (boiling range 30-200 ᵒC), kerosene (175-300 ᵒC) and paraffin oil (275-400 ᵒC). The residue from the atmospheric distillation column – the mazut – boils at temperatures above 350 ᵒC. It is separated in the next stage of oil processing, which involves distillation under reduced pressure. Vacuum and the addition of steam significantly reduce the boiling points of hydrocarbons. This allows them to be separated from each other without the risk of thermal decomposition. The products of vacuum distillation of mazut are vacuum gas oil, paraffinic distillates and an intermediate product for further processing.
- Catalytic cracking – individual crude oil fractions contain mainly long-chain aliphatic hydrocarbons. In industry, the greatest demand is for petrol, which is a mixture of hydrocarbons with chain lengths of between 5 and 12 carbon atoms. Catalytic cracking, during which the carbon-carbon bonds in long-chain molecules are broken, helps obtain such compounds. Cracking is usually initiated thermally or catalytically. The main reactions occurring during catalytic cracking are the breaking of C-C bonds in alkanes, dehydrogenation of naphthenes, ring breaking of naphthenic hydrocarbons and polymerisation of alkenes.
- Reforming – reforming is another petroleum refining process, which aims to extract as much petrol as possible. During this process, hydrocarbons with straight carbon chains in their molecules are transformed into branched and/or aromatic compounds. Reforming is applied to gasoline distillates, as well as to the products of cracking of the heavier petroleum fractions. This process is extremely important because, under its influence, petrol octane number is increased (isomerisation, dehydrocyclization, aromatisation), which increases its quality significantly. In addition, significant amounts of hydrogen gas are produced during reforming. It is used in hydroprocesses such as hydrorefining and hydrocracking.
Natural gas
Natural gas is another non-renewable fossil fuel of energy importance. It is a gaseous fuel. It is often found with oil deposits – either as a separate fraction or dissolved in it. Depending on the location of the reservoir, there are several types of natural gas: high-methane, nitrogen-rich, dry and wet.
The first of them is the most important, as it contains the most methane in its composition, up to 98%. In addition, natural gas also contains (in varying amounts) ethane, propane, carbon monoxide, carbon dioxide, nitrogen and helium. Importantly, natural gas has no odour. In order to detect its leakage quickly, it is odoured with special substances so that it can be easily sensed.
The natural gas extracted from the field is quite heavily contaminated. Thus, in order for it to be used by consumers, it must undergo purification processes. Natural gas processing is based on them.
The key stages of this process include:
- Dehydration – consists of eliminating the moisture contained in the gas. Some contaminants are also removed along with it. The water vapour in natural gas causes corrosion of pipelines and also leads to the formation of hydrates, which is why it is necessary to dry natural gas before releasing it into the network. The separated liquid is called formation water. It is taken to special storage facilities and then further purified. The methods used to dehydrate natural gas are absorption (glycols), adsorption (calcium and magnesium chloride salts) and membrane techniques.
- Carbon dioxide removal – this process is often referred to as decarbonisation. Along with sulphur, carbon dioxide is one of the more harmful pollutants in natural gas. CO2 is an acidic gas. It readily reacts with the water vapour in the gas and forms carbonic acid. Although it is a low-potency acid, it has a negative impact on, among other things, gas transport systems due to its corrosive properties. Therefore, decarbonisation of natural gas is necessary.
- Desulphurisation – the presence of sulphur in natural gas, e.g. in the form of hydrogen sulphide, is very detrimental. It not only affects the quality of the gas as a fuel, but also has poisonous and corrosive properties. Hydrogen sulphide is a highly toxic gas. Eliminating it from natural gas deposits is also an important step towards protecting the environment. Desulphurisation processes typically use physical adsorption and chemisorption methods. Activated carbon and zeolites, among others, are satisfactorily effective as adsorbents removing H2 Absorption usually takes place by chemical reaction with natural masses (e.g. bog iron). One of the most effective methods of removing hydrogen sulphide is oxidation against a catalyst, the so-called Claus process. It involves the recovery of elemental sulphur from the H2S contained in the gas.
Peat
Peat is a fossil fuel with unique properties. It is considered the ‘youngest’ of the fossil coals. Peat formation involves the transformation of accumulated debris, mainly plant material. These processes are known as peatification. They occur at high moisture content and with limited access to oxygen. Peats are divided into homogeneous and heterogeneous, which are characterised by a mixed composition. Peat is separated from lignite by a conventional limit of elemental carbon content of 65% by weight. After extraction, peat is divided into three fractions, depending on grain size: small, medium and large. Freshly extracted peat is usually highly acidic, so additives such as dolomite powder are often used to reduce this acidity.