Polyolefin films, such as polyethylene (PE) and polypropylene (PP), are widely utilized in packaging, agriculture, and other industries. However, these materials often require functional improvements to meet application-specific needs. Additives for Polymers are essential enhancements that enhance the usability, safety, and appearance of polyolefin films. PCC Chemax Inc., a leading provider of specialty chemicals, offers a range of innovative additives that cater to these requirements.
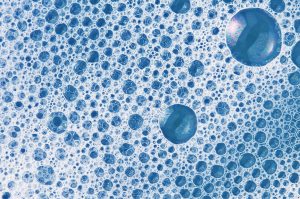
PCC Chemax has a long history in developing polymer additives, with their first product being introduced in the 1970s. PCC Chemax’s Polymer Additives group offers technical support in addressing additive solution challenges customers present. In addition to introducing new materials including antistats, antifogs, lubricants, pigment dispersants, and slip agents, the technical staff is well versed in a variety of polymers including PVC, PET, PE, PU, LLDPE, LDPE, HDPE, and PP.
With hundreds of chemistries available, the technical department can explore non-traditional molecular structures and substantiate results with standard industry testing methods. They address traditional industry issues as well as the most recent challenges that include long-term antistatic protection and corrosion inhibition.
Recognizing client’s needs, PCC Chemax developed the technology of using silica as a carrier for liquid products, creating powdered versions of most antistats and antifogs in our portfolio.
Understanding Antistatic Additives
Antistatic additives reduce the buildup of static electricity on polymer surfaces, a phenomenon that can cause dust attraction, handling difficulties, and even safety hazards in environments prone to sparks. PCC Chemax offers both internal and topical (external) antistat agents in a variety of chemistries and physical forms to meet the most specialized requirements.
Internal antistatic additives are incorporated during polymer processing. These additives migrate to the surface, forming a water-attracting monolayer that dissipates static electricity. The majority of the PCC Chemax antistat portfolio belong to this group. Offerings include ethoxylated coco, tallow and stearyl amines (respectively Chemstat® 122, Chemstat® 182, Chemstat® 273-E). Ethoxylated amines show excellent performance in PE, PP and PS/ABS, may also improve pigment dispersibility and have broad FDA approval. Another offered chemistry is lauric diethanolamide represented by Chemstat® LD line (Chemstat® LD-100, Chemstat® LD-100/60DC). Chemstat® LD is recommended as an antistat when relative humidity conditions of <40% are present and when ethoxylated amines cannot be used.
In addition to amines and amides, PCC Chemax offers nonionic proprietary surfactant mixtures including Chemstat® 1880, Chemstat® 1890, Chemstat® 1900 and Chemstat® 1910. These are liquid or flaked solid containing no phenol derivatives or amine-based components, providing antistatic performance and several may be used in indirect food contact applications.
All of these products are or may be available in an easy-to-handle powder form.
Topical (external) antistatic agents are applied after processing to provide temporary antistatic properties. PCC Chemax offers Chemstat®3820 which is a water soluble cationic antistat suitable for external application which functions at low concentrations and is readily soluble in multiple diluents.
Exploring Antifog Additives
Antifogs prevent the formation of water droplets on the surface of a film. This is achieved by incorporating an additive which will agglomerate water droplets allowing it to sheet off the polymer surface. For greenhouse applications, antifogs minimize or prevent microlensing which protect plants from damage. The best antifog for a specific application will depend on polymer type, film thickness, use temperature, and lifetime of the film. FDA requirements should be identified prior to evaluation.
PCC Chemax offers the Chemstat® AF series, which comprises a wide range of antifog products. Chemstat® AF-476 prevents fogging of PVC that require high heat tolerance. Chemstat® AF-322 is effective in both film and molded products and may be used for polypropylene resins. The material provides both hot and cold antifog performance. Chemstat® AF-687 is recommended primarily as an external antifog for PS films and performs as an internal hot and cold antifog in PE resins.
Several products are, or may be, available in an easy-to-handle powder form.
Antistatic and antifog additives offer a number of benefits. They improve aesthetics by preventing the accumulation of dust and water droplets, providing a clean appearance, protecting plants and allowing the consumer a clear view of food products. They also extend the durability of films by protecting them from damage and environmental degradation, thus extending their service life.
In addition, these additives are versatile and suitable for a wide range of applications across a variety of industries.
Why polymers need lubricants?
Lubricants are used as processing aids particularly in rigid and flexible PVC. They can either be incorporated into the polymer compound or applied externally to the polymer surface. A lubricant works by providing a considerable decrease in resistance to movement of chains or segments of a polymer, without disproportionate change in observable properties. Ease of internal rotation is the key to polymer flow. Internal lubricants, compatible with the polymer, reduce melt viscosity and processing energy. External lubricants, incompatible with the polymer, reduce both polymer-to-polymer as well as polymer-to-metal friction.
Selecting the right lubricant involves considering chemical composition, polarity, melt properties, compatibility, and interactions with other additives. For example, ethylene bis-stearamide acts as both an internal and external lubricant but it is not a preferable choice for clear film application because could haze the film. For clear film, glycerol monostearate is recommended.
PCC Chemax offers Glycerol Monostearate in different forms and monoester composition. Chemstat® G line includes products in this chemical family. GMS works not only as a lubricant, but also as mold release, internal antistat and antifog. Maxomer® Lube EBO is a fatty acid amide used primarily as a slip agent in film manufacturing, particularly suitable in polymers like PVC, polyamide, polycarbonate and polypropylene. This chemistry is often used to raise the melt flow of polystyrene and imparts antiblocking properties to a variety of resins. Maxomer® Lube-FESA, ferric stearate, performs as a photo degradation agent in polyolefins. Maxomer® Lube-E2SA-B is effective as a lubricant in PVC, polystyrene, ABS, and some engineering resins. It also functions as a mold release agent in PVC, polystyrene, and polyesters. The high molecular weight chemistry also serves as a pigment dispersant in polyolefin processing.
Slip agents enhances performance and efficiency.
The most commonly used slip agents are amides, such as oleamide (Chemstat® HTSA#18), erucamide (Chemstat® HTSA#22-20M) and stearyl erucamide Chemstat® HTSA#3/BEAD). These agents are categorized based on their migration rates: “fast bloom” agents like oleamide migrate quickly to the surface, while “slow bloom” agents like erucamide migrate more slowly. This migration helps to overcome the natural tackiness of polymers, making them easier to handle and process.
PCC Chemax also offers Chemstat® HTSA#1, a secondary amide (oleyl palmitamide), which is a nitrogenous organic compound, designed for use as a slip additive for thermoplastics – particularly BOPP film.
Slip agents are particularly beneficial in applications involving thin films, where high friction can cause issues during winding, bag production, and packaging operations. By reducing friction, slip agents improve the efficiency and reliability of these processes
Conclusion
Antistatic and antifog additives, slip agents and lubricants play a crucial role in optimizing polyolefin films for multiple applications. By addressing challenges like including static buildup and fogging, these additives enhance functionality, safety, and aesthetics. As industries demand more sustainable and efficient solutions, ongoing research and innovation will continue to refine these essential materials, shaping the future of polyolefin-based applications.