Static electricity is a common physical phenomenon, often observed during everyday activities. This can be manifested, for example, by an electrical spark while touching various objects (e.g. a shopping cart, a handle, a car), or even a human, or while combing hair - when they stand up.
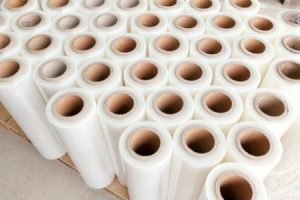
Static electricity can also occur on a much larger scale and cause serious, negative effects. The spark resulting from electric charges can lead to a fire or even explosion of flammable materials, as well as impede the course of many production and processing processes. Therefore, it is definitely worth to learn more about the specificity of this phenomenon, as well as ways to counteract its occurrence.
Static electricity – what is it about?
Static electricity is a build-up of electric charges on materials with low conductivity and high surface resistance (1014 – 1018 Ω). This applies, inter alia, to polymeric materials, such as:
• polyethylene terephthalate (PET),
• polycarbonate (PC).
Accumulated electric charges result in spark discharges that impede the use of plastic products. Static electricity, however, has an adverse effect not only on end users of polymers. It also affects the processing and production of polymers. This phenomenon reduces the speed of the technological process, generates material losses, causes a contamination of the product and accelerates its decomposition, as a result of which toxic compounds are released. Stationary electric charge can occur while pouring liquid or pouring non-conductive loose materials, unwinding tapes or foil from a drum, walking on an electrified surface, or putting on and taking off clothes.
How to avoid static electricity?
Static electricity can be minimized or even completely eliminated by the use of appropriate antistatic additives, such as surfactants reducing the polarization of plastics. Antistatic agents reduce the surface resistivity of materials, which causes the charge to dissipate, and as a result reduces the occurrence of the adverse phenomenon.
External and internal antistatic agents – how do they differ?
Antistatic agents can be divided according to their application into two groups: external and internal antistatic agents. They differ from each other in the method of their application, the mechanism of action, and the duration of the antistatic action.
The external antistatic agents are applied to the surface of the finished plastic. Techniques such as spraying and dipping are used here. The duration of the antistatic action of this type of compounds is very short, due to their abrasion under the influence of mechanical factors. These compounds lose their activity after just 6 weeks and in this respect, they do not equal the properties of internal antistatic agents.
The internal antistatic agents, which are added to the plastic during its processing, like other types of polymer additives, work completely differently. After 24-48 hours from the extrusion process, they migrate to the surface of the material, forming a hygroscopic film that attracts water. The created layer has a conductive function, as it discharges static electricity and reduces the level of plastic charge.
The antistatic effect in the case of internal antistatic agents is long-lasting (usually over one year). It is the migration of internal antistatic agents that ensures a longer period of their activity – the layers that are abraded from the surface of the polymer are replaced.
Chemical compounds with antistatic properties
Depending on the type of plastic, antistatic agents with various chemical structures are used in the industry. Basically, there are two groups – ionic and non-ionic additives. The first group is recommended for polymers with relatively high polarity or for materials that do not require too high temperatures when processing the film. The ionic antistatic agents are such compounds as:
• cationic compounds, which include quaternary ammonium salts,
• anionic compounds – these are mainly compounds containing phosphorus (derivatives of phosphoric acid (V), phosphates (V)) – used for polyvinyl chloride, as well as sulphur-containing compounds (sulphates (VI), sulphonates) – used for polymers such as polyvinyl chloride and polystyrene.
The second group are non-ionic additives, which are mainly recommended for polyolefins. Non-ionic antistatic agents are amide derivatives (alkoxylated amides), amine derivatives (alkoxylated fatty amines) and glycerol esters.
What are the characteristics of an effective antistatic agent?
Regardless of the mechanism of action, antistatic agents should have several features that ensure their high efficiency. These features are primarily:
• hydrophilic and hygroscopic properties,
• the ability of ionization in water – the presence of ions increases the water’s conductivity,
• the ability to migrate towards the surface of the material.
Plastics in the food industry
The main raw material used in the production of packaging film in the food industry is polyethylene. Polyethylene (PE) is a polymer characterized by tensile strength, lack of smell and taste and a waxy structure with a milky colour. Thanks to these properties, it is used in the production of, among others: foils, packaging, containers, bottles, as well as drinking water pipes. The plastic has a surface resistance of around 1015Ω, which makes the electrostatic phenomena evident to a large extent. For this reason, during the production of various polyethylene elements, it is necessary to use agents preventing the accumulation of charges.
What surfactants can be used as antistatic agents?
Antistatic agents that are commonly used in polyethylene are internally applied compounds. The product portfolio of the PCC Group includes such products as: Chemstat 122, Chemstat PS-101, Chemstat G118/9501, Chemstat 3820 and Chemstat LD-100/60DC. These substances effectively reduce the surface resistance even to the value of 1010Ω, which guarantees an excellent antistatic effect, thus eliminates the problem of the build-up of electrical charges on the surface of the material and spark discharges. Some of them can also be used in the production of packaging for the food industry.
Particular attention should be paid to the specialist product, which is Roksol AZR. This antistatic agent is dedicated to stretch film used in manual wrapping of goods on pallets. The product has excellent anti-static properties, as it lowers the surface resistance to 108Ω.
Antistatic agents – addition or necessity?
The use of antistatic agents in the production of plastics is definitely a necessity. Their presence is essential as they facilitate the production process and prevent dangerous spark discharges. They also provide additional benefits such as limiting the accumulation of dust on plastic objects that is attracted by too much electric charge. Due to the various mechanism of action of antistatic agents, it is possible to adjust them to specific conditions of the production process and maximize the final effect.
Interesting fact
In 1937, static electricity caused the fire of the largest Hindenburg airship in the history of Germany. It contained 200,000 m3 of flammable hydrogen. During the landing, most likely due to an electric spark, the gas ignited, causing the airship to burn down completely.
- https://mfiles.pl/pl/index.php/Antystatyki
- Rabek J. (2008), Współczesna wiedza o polimerach, Wydawnictwo Naukowe PWN, Warszawa
- https://www.kierunekchemia.pl/artykul,59794,srodki-antystatyczne-po-co-sa-dodawane-do-tworzyw-sztucznych.html
- https://www.plastech.pl/wiadomosci/Srodki-antystatyczne-po-co-sa-dodawane-do-tworzyw-13246
- Duda I. (red.) (1995), Słownik pojęć towaroznawczych, Wydawnictwo Akademii Ekonomicznej w Krakowie, Kraków