The term ‘construction chemistry’ had once been used only for additives to concrete mixes. Over the years, the industry has developed significantly, and the definition itself has evolved. Currently, in this category of chemicals, a whole range of substances necessary both during typical construction and finishing works is available. Many new mixtures for mortars and concrete have been developed as well as countless auxiliary formulas such as paints, adhesives, silicones, impregnations, mortars and plasters.
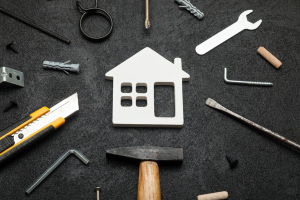
Cement
Cement is a hydraulic binder whose properties cause it to harden when mixed with water. It is used in the production of mortars and concretes. The ingredients in cement include are elements that are common in nature, e.g., calcium, silicon, aluminium, iron and oxygen. The raw materials used in cement production are natural minerals such as limestone, marly limestone, marl and clay minerals. Each of them is sourced in opencast mines that most often are located next to cement plants. The basic ingredient of cement is cement clinker, and the extraction and initial processing of raw materials is a key technological phase of the manufacturing process, as it directly affects the maintenance of its consistent composition and quality. The clinker is responsible for the binding properties of cement. The raw materials for clinker firing can be various mixtures, e.g.:
- chalk 53.42% + marl 46.58%,
- limestone 88.69% + shale 10.06% + iron-bearing loam 1.27%,
- limestone 87.23% + shale 5.01% + iron-bearing loam 7.76%.
The basic oxides that make up the clinker are SiO2, Al2O3, Fe2O3. During the kiln firing process, these oxides react with each other under the influence of high temperature to form basic clinker minerals, i.e.:
- tricalcium silicate Ca3SiO5, the so-called alite with the technological formula C3S,
- dicalcium silicate Ca2SiO4, the so-called belite C2S,
- tricalcium aluminate Ca3Al2O6 – C3A,
- tetracalcium aluminate Ca4Al2Fe2O10, the so-called braunmillerite C4AF
The composition of cement defines its type: Portland cement, a metallurgical cement with the addition of slag and pozzolanic cement with the addition of pozzolan. Portland cement is obtained by grinding cement clinker with gypsum in cement mills. Portland clinker is composed of 55–58% C3S, 12–19% C2S, 5–12% C3A and 3–7% C4AF. The addition of gypsum regulates the cement setting time, because without the presence of sulphates during hydration, cement hardening would proceed almost immediately after the addition of water.
See the range of concrete additives and admixtures from the PCC Group. See also: microsilica.
Mortar
Mortar is a mixture that should have good binding properties, adhesion to the substrate, strength, workability and technical parameters appropriate to the current needs, such as frost resistance, water absorption and heat protection. Depending on the type of binder present in the mortar composition, it is divided into cement, cement-lime, gypsum and gypsum-lime. Portland cement is most often used for cement mortars, and their use includes building walls and foundations, underlayments, floor underlays, etc. Such mortars harden in water as readily as they do in the open air. not only in air, but also Lime mortars harden as a result of carbonisation of calcium particles under the influence of carbon dioxide from the atmosphere. Slaked lime, which is a component of this mortar, reacts with CO2 molecules, resulting in a calcium carbonate molecule and a water molecule. Due to the slow course of this process, artificial drying with hot carbon dioxide gases is sometimes used. Lime mortar has good heat-insulating properties, but it is not very resistant to weather conditions and deteriorates quickly. Cement-lime mortars combine the positive features of both types mentioned above. They harden quickly and have high strength and good workability. Gypsum or gypsum-lime mortars are also used, but they are not very resistant to moisture and are usually used for plastering walls and ceilings indoors, making finishings and fixing carpets.
House insulation
The insulation system should consist of several layers, i.e., mortar or adhesive, thermal insulation material, mechanical fastening element, reinforcing layer, plaster, primer, façade paint and filling material. Chemically, the adhesive mortar consists of a mixture of polymer and cement. Thermal insulation materials include, e.g., polyurethane foams (read more about spray insulation), phenolic foams and extruded polystyrene. Traditional cement-lime plaster consists of cement, calcium, sand and water, and the priming agents that increase adhesion are synthetic resin dispersions and grains of mineral filler, e.g., quartz or carbonate.
See the range of PIR thermal insulation panels from the PCC Group.
Paints and varnishes
Nowadays, a nice colour is not the only indicator of good paint. Customer demands are increasing – the paints must be quick-drying, resistant to abrasion, providing a perfect cover with just one coat. All these features require the use of appropriate ingredients. The basic ingredients of paints are:
- binders that cause the formation of a membrane-forming film on the painted surface. They are responsible for such properties as gloss, durability, adhesion, resistance to weather conditions, strength and flexibility. Synthetic or natural resins, such as polyurethanes, polyesters, silanes, epoxy resins and oils, are most commonly used as binders;
- diluents, designed to dissolve the polymer and lower its viscosity. This substance must evaporate easily during drying; moreover, it affects the product application during painting. Two main types of thinners are used – water for water-based paints and a combination of organic solvents for oil-based paints. Such mixtures are most often created by combining aromatic compounds – xylene derivatives, alcohols and ketones;
- pigments have a rather obvious effect – they give the right colour. Both natural pigments, including clays, silicas, calcium carbonate and talcs, and synthetic pigments such as calcined clays, barium sulphate, precipitated calcium carbonate and pyrogenic silicas, are used to give colour. Some of the pigments act also as fillers, i.e., relatively cheap substances designed to increase the volume of paint and strengthen its structure, while reducing the manufacturing cost. This group includes diatomaceous earth, talc, lime, barite and clay;
- modifiers are added in small amounts and have a strictly defined task in the formulation. They can affect various properties of the finished product, e.g., the surface tension, stability, foaming or freezing point.
Paints can be classified according to their binder:
- acrylic, where the binder is a water dispersion of acrylic resin;
- latex, where the binder is rubber;
- vinyl, where the binder is polyacetate or polyvinyl chloride;
- glue, where the binder is vegetable or animal glue;
- silicate, where the binder is potassium water glass;
- silicone, where the binder is silicone resin.
Unlike paint, varnish is made from hard and linear polymer. It is designed to create a transparent or coloured coating for decorative or protective purposes. Its layer is supposed to prevent mechanical damage and moisture penetration. They are classified into two groups – solvent and water-based varnishes. Polyurethane, nitrocellulose resin, drying oils, natural and synthetic resins can be used during the manufacturing process of the solvent-based varnishes. Water-soluble varnishes, on the other hand, are produced using acrylic, water-based polyurethane and their mixtures.
Glass
An amorphous substance with mechanical properties similar to a solid, formed as a result of supercooling of molten raw materials, mainly minerals and other inorganic compounds, without the crystallisation of components. Due to the lack of spatial arrangement of the structure, glass is similar to a liquid, but its rigidity and fragility bring it closer to a solid. The glassy state in which glass occurs is thermodynamically unstable. The raw materials used in glass production are:
- glass sand (quartz) – source of silica SiO2
- soda, which is a source of basic metal oxides, mainly Na2O
- limestones CaCO3, magnesites MgCO3, dolomites CaCO3MgCO3, which are the source of calcium and magnesium oxides
- borax – source of boron oxide B2O3
- sodium-potassium feldspars containing aluminium oxide
- titanium dioxide TiO2 and zirconium dioxide ZrO2
During the production of glass, raw materials containing pigments are also used, such as:
- copper oxide Cu2O to obtain blue and green colours
- iron oxides – yellow, amber, blue-green depending on the degree of iron oxidation
- cobalt compounds – blue
- gold compounds – from pink to purple
Besides that, decolonising compounds are sometimes used to accelerate melting or clarification of the glass mass.
Chemical energy
Items such as batteries, but also the potted plants in your home, are examples of everyday, ordinary chemical reactions. Chemical energy can be transformed into another energy as a result of a chemical reaction. The above-mentioned batteries are actually electrochemical cells where the transition of ions between the electrodes generates electricity. On the other hand, plants undergo the process of photosynthesis, during which the influence of an energy source, i.e., solar radiation, transforms carbon dioxide into oxygen. Burning, e.g., of wood in a fireplace, also releases chemical energy, in the form of heat.
Read more: how are batteries manufactured?
The Internet and chemistry
It seems that it is difficult to physically the Internet and chemistry. However, one should think about the carbon footprint, which has become a topic of intense discussion in recent years. It turns out that the global network emits huge amounts of gases such as carbon dioxide, methane, nitrous oxide and other greenhouse gases. Servers, data centres, switches and routers have the greatest impact, although their use is diminishing as a result of replacing analogue technologies with fibre optics. Today, manufactured optical fibres are made of glass fibres and plastics, e.g., silicon tetrachloride.