Modification of polymeric materials is one of the most compelling fields of science that is related to the processing of plastics. Given that polymeric materials are virtually unavailable in a non-modifiable form, the issue is both interesting and highly significant. A huge number of diverse additives are commercially available that are used to modify the basic properties of polymers. The most essential additives include plasticisers, whose task is to ensure the finished product is flexible.
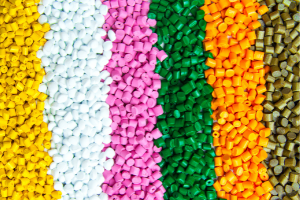
What do we know about plasticisers?
Plasticisers are usually medium to high polar chemical compounds added to a polymer during processing. As regards the chemical aspect, a plasticiser effectively wets the polymer grain and enters the structure of the compound, thus expanding the polymer chains. This creates a flexible material. Such a modification of plastics translates into lower strength and hardness of the material.
Plasticisers required for PVC production
Approximately 80% of global plasticiser production is handled by producers of flexible polyvinyl chloride, i.e. PVC. Suc7h a high share of one plastic is due to the chemical structure of PVC, which is readily affected by plasticisers. Consequently, the modification of PVC is highly effective and economic, and most importantly, reversible. Flexible PVC may be successfully recycled, and admixtures of used material may be employed in the manufacture of new products. Interestingly, even rigid PVC used in the production of sewage pipes or window profiles uses small amounts of plasticisers in order to facilitate processing.
PVC is a noteworthy material due to its unique properties. Unmodified polyvinyl chloride is a flame-resistant material due to the high chlorine content (approx. 57%). The addition of conventional plasticisers increases the flammability of the material due to the high flammability of the modifying agents. What if you need to obtain a product that is both flexible and non-flammable? Those requirements are addressed by phosphorus chemistry, more specifically, compounds called phosphates.
Phosphates – a key additive for flexible and non-flammable materials
Additives based on phosphorus chemistry combine the functions of a plasticiser and a flame retardant. Thus, phosphates become a crucial additive for special applications that require both efficient plasticisation and effective flame retardancy. Additional advantages of these plasticisers include low viscosity and the form of a homogenous and clear liquid. This parameter is essential in the production of transparent products such as membranes, technical films and curtains. Flame-retardant plasticisers replace solid additives that would cause the fogging of the finished material. Another major issue is the low migration of phosphates from the material, which improves the performance of the finished product.
Flame-retardant plasticisers belonging to the phosphate group are used more and more frequently in other plastics. Due to their versatility, they can be used in the processing of EVA or EPDM (cable and wire insulation). Phosphates are increasingly met with interest from the automotive and furniture industries, where they are used to modify thermoplastic elastomers such as TPU, TPE or PUD (coated fabrics, artificial leather, projection screens).
Where should I look for additives for plastics?
Today’s market requirements are not only about the ability to efficiently plasticize the material or a high flame retardancy profile. The changing legal regulations dedicated to the plastics segment impose increasing demands on producers concerning the generation of toxic fumes and gases and heat release during combustion. Other advantages of additives used are also emphasised such as the ecological aspects of a product or the effect of plasticisation at low temperatures. The latter has become a determinant contributing to changes in the technology of products developed by the R&D Department of PCC Rokita.
In recent years, the Roflex series plasticiser portfolio has been extended to include products that combine several desired functions simultaneously. In addition, a major challenge was to propose solutions that would be adapted to minimise the negative impact on the environment as well as human health and life. The latest products in the Roflex series included in the portfolio of PCC Rokita include:
- Roflex T70L – a plasticiser developed especially for products featuring high requirements concerning environmental performance. It has no GHS hazard classification, i.e. no-labelling;
- Roflex T120 – an additive with a less severe environmental classification, it allows the avoidance of the ADR classification in transport systems for the finished product;
- Roflex T45 – the first modified phosphate in the PCC portfolio to ensure high plasticisation at low temperatures. It is characterised by a lower level of smoke generation during the combustion process. No-labelling.
In reference to the title, the products of PCC Rokita ensure flexibility and more!
Patryk Juszczak
Technical Support Manager
PCC Rokita SA