One of the most interesting construction solutions used on a mass scale in recent years for the covering of walls and roofs in various types of facility is the sandwich slab. Until recently they were used almost exclusively in the construction of halls, warehouses and industrial facilities, but nowadays they are becoming an attractive alternative to other traditional building materials. What lies behind the growing popularity of sandwich panel cladding, where is it used and how can it be effectively combined?
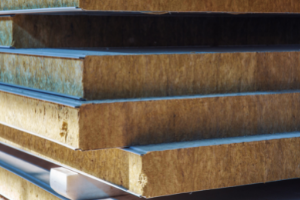
Popularity and use of sandwich slabs
Façade sandwich slabs, an increasingly popular choice due to their numerous construction and installation advantages, comprise special metal panels with enhanced thermal and acoustic insulation. They are used for all kinds of light industrial, warehouse, sports, entertainment and commercial buildings. The durability, aesthetics and possibility of fast installation mean the sandwich slab, popularly referred to as a sandwich panel, finds recognition in other areas of modern construction.
Being able to arrange this type of cladding vertically and horizontally makes it a popular solution for the walls and roofs of various types of building. Another advantage is the possibility of free shaping the modules, allowing them to be used effectively in the construction of any building type. In addition to traditional sandwich panels there are also cooling panels available on the market, with special thermal properties that are convenient for the construction of cold storage and other low-temperature rooms.
How is a sandwich slab constructed?
Although the structure of individual sandwich panels may vary considerably due to their application and manufacturing technology adopted, their basic elements usually involve:
- external cladding made of profiled steel sheet,
- an internal structural core that also acts as a thermal and acoustic insulator.
The insulating core usually consists of several sheets which, depending on the manufacturer and the application of the cladding, can be made of mineral wool, polyurethane foam, polystyrene and/or other materials. The manufacturing process for a sandwich panel involves joining its individual layers with dedicated chemical products – usually polyurethane adhesives, such as RokaPur PR1K_15.
Advantages of sandwich slabs
The universal application of the sandwich slab, combined with its widespread availability and the high durability of the buildings where it was used, means the sandwich slab finds many supporters. More and more industries are using them as a basic building material, appreciating their structural, aesthetic and functional qualities. What are the main advantages of façade sandwich slabs?
Architectural freedom
Modern production technology and the wide range of available solutions make it possible to choose panels which perfectly match the requirements of a particular project and the architectural landscape. This makes the facility even more functional and better suited to the investor’s needs.
Wide range of panels available
Manufacturers offer sandwich panels in a range of sizes, thicknesses and fillings. This allows the investor to select the cladding type with optimal parameters for the building’s functionality.
Vertical and horizontal installation
Modern sandwich modules can be used both for cladding external walls of buildings and roofs. In both cases, their use ensures a high level of thermal insulation.
High level of sound insulation
Apart from their thermal insulation, sandwich panels also ensure good levels of soundproofing for facilities, protecting the surroundings from excessive noise. This feature becomes particularly important in noisy production environments or shopping centres.
Fire safety
The use of top-quality materials with the appropriate certificates and approvals ensures that façade sandwich panels have a high level of fire safety. Both the exterior sheets and the central insulation layer are made of non-flammable and flame-retardant materials, such as mineral wool, PUR foam or polystyrene.
Easy and fast installation
Another unquestionable advantage of the sandwich panel is the fast and trouble-free installation, requiring just screwing the cladding to the building’s structure using self-drilling screws. As a result, the exterior cladding of a large hall or shopping centre can be completed in an incomparably shorter time than with traditional building materials.
Read more about sandwich panel installation: www.products.pcc.eu/en/blog/installation-of-sandwich-panels-step-by-step-to-a-durable-structure/
Low weight
The light weight combined with high load resistance makes a sandwich slab an ideal solution from the point of view of installation and possible expansion of the structure. At the same time, the energy-efficient parameters of the panel cladding mean that its use significantly reduces the operating costs of the facility.
Effective appearance and colours
The availability of sandwich panels in an extremely diverse range favours the matching of the external aesthetics of the facility to the investor’s requirements and spatial conditions. The wide range of architectural solutions combined with the high resistance of sandwich panels make them suitable for both typical and most non-standard applications.
What chemical substances are used to manufacture sandwich panels?
To ensure that sandwich panels allow the investor to benefit from their full structural, insulation and aesthetic advantages, the panel production process must be carried out using appropriate technologies and materials. This applies particularly to the joining of individual layers. It is particularly important to choose the right polyurethane adhesive to ensure the durability of any joint. At the same time, the joint should be sufficiently flexible and resistant to vibrations, while the adhesive itself must adhere properly to the substrate. In such conditions, two-component adhesives, such as Ekoprodur 1331B2 from the PCC Group – a manufacturer of special chemical substances for industry – prove to be the best solution. Its main advantage is the ability to bond polystyrene, mineral wool and polyurethane panels. Single-component adhesives such as RokaPur PR1K_15 can also be used to bond the above materials to the sheet.
Read also about PIR thermal insulation panels: https://www.products.pcc.eu/en/pir-thermal-insulation-boards/
Summary
The increasing scale of application of sandwich panels in industrial construction results in growing interest in this technology among investors. The indisputable advantages of façade sheets, possible thanks to modern production technology and the use of high-quality components, make it a functional, inexpensive and much more convenient alternative to traditional building materials. Today it is certainly one of the most effective construction technologies and, if only for this reason, it is worth following the development of the sandwich panel market in the years to come.
- Kopyłow O., Sieczkowski J., Budynki z obudową z płyt warstwowych – diagnostyka stanu technicznego obudowy, Instytut Techniki Budowlanej, Warszawa 2023.
- Murkowska M., „Płyty warstwowe lekkiej obudowy w nowych rozwiązaniach technicznych i architektonicznych”, Materiały Budowlane, nr 2/2002, s. 28–29.
- Polski Komitet Normalizacyjny, PN-EN 14509:2013-12: Samonośne izolacyjno-konstrukcyjne płyty warstwowe z dwustronną okładziną metalową – Wyroby fabryczne – Specyfikacje, PKN, Warszawa 2013.
- Sawicki J., „Konstrukcyjno-izolacyjne płyty warstwowe”, Izolacje, R. 11, nr 7–8, 2006, s. 63–66.
- Sawicki J., Płyty warstwowe w sztywnych okładzinach metalowych. Przewodnik dla inwestorów, architektów i wykonawców, Dom Wydawniczy Medium, Warszawa 2010.
- Allen H. G., Analysis and Design of Structural Sandwich Panels, Pergamon Press, London 1969.
- Davies J. M. (red.), Lightweight Sandwich Construction, John Wiley & Sons, Chichester 2008.
- Makweche D., Dundu M., „A review of the characteristics and structural behaviour of sandwich panels”, Proceedings of the ICE – Structures and Buildings, vol. 175, no. 12, 2022, s. 965–979.
- DIN EN 14509:2014-07, Selbsttragende Sandwich-Elemente mit beidseitigen Metalldeckschichten – Werkmäßig hergestellte Produkte – Spezifikation, Beuth Verlag, Berlin 2014.
- Möller R., Pöter H., Schwarze K., Planen und Bauen mit Trapezprofilen und Sandwichelementen: Gestaltung, Planung, Ausführung, 1. Auflage, Ernst & Sohn, Berlin 2011