Crude oil is indispensable for the functioning of many industries and also plays the role of an extremely important geopolitical factor. Like natural gas, it belongs to naturally occurring hydrocarbons whose deposits can be found in numerous places around the world.
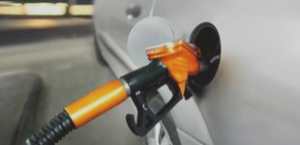
These raw materials are processed in refineries for various products, such as:
a) Liquid gas (LPG)
b) Motor fuels (petrol, kerosene, diesel oil)
c) Heating oils
d) Road and industrial asphalt
e) Hydrocarbon raw materials for various syntheses
f) Petroleum coke
g) Solid petroleum hydrocarbons (e.g. paraffin)
In addition, the products of the fuel industry play the role of raw materials for the preparation of various chemical products, including pharmaceuticals (paraffin obtained from heavy oil fractions used as a laxative), fertilizers (phenol used for the production of plant protection chemicals), solvents (petroleum ether and acetone) and plastics (polyolefins).
Crude oil processing
In the industry, over 90% of crude oil is processed into gasoline, oils and asphalt. The sodium hydroxide solution, i.e. soda lye, is of great importance in this process. It is used to remove impurities such as sulfur compounds and carbon dioxide. Their elimination is a key stage in the oil refining process, necessary to meet the legal requirements for the content of these compounds. Soda lye is also used in the refining of end products obtained after processing of crude oil. There are several basic processes:
a) Distillation – a process consisting in the separation of crude oil into fractions differing with the boiling point. In this way, several raw materials are obtained, such as dry and wet gas, gasoline, kerosene, diesel oil, mazout and gudron.
b) Catalytic cracking – involves the use of a catalyst (mainly zeolites) to break down heavy oil fractions into lighter fractions. In this way, a relatively large amount of high-quality gasoline is obtained.
c) Catalytic reforming – a catalytic conversion of low octane gasoline into high-octane gasoline in the presence of a platinum catalyst. The main products of this process are: hydrogen, refinery gas, LPG, iso- and n-butane.
d) Hydrocracking – catalytic processing of heavy oil fractions, mazout and gudron under hydrogen pressure into lighter fuels. The gasoline, kerosene and diesel fuels are obtained in this way.
e) Pyrolysis – a breakdown process of heavy oil fractions in the presence of water vapor. In this way, pyrolysis gasoline, oil and tar are obtained.
f) Alkylation – involves the reaction of olefins with isobutane, resulting in the formation of isoparaffins with higher molecular weight and octane number. This process involves reactions carried out at low temperature and in the presence of a catalyst. The most commonly used catalyst is sulfuric acid. In the PCC Group, sulfuric acid is obtained by contact process, which gives it very high purity. The sulfuric acid thus obtained can be used in the processes of purifying oils, kerosene, paraffin and gas drying.
Types of fuels
Fuels can be divided according to their origin (natural and artificial), calorific value (high and low calorie), as well as their state of aggregation (liquid, gas and solid). Each type has different properties and a range of applications.
Liquid fuels – gasoline
The most important liquid fuels obtained from crude oil include: petrol, kerosene, diesel and heating oils. Gasoline is a crude oil fraction that boils at a temperature of about 40oC to 200oC. It is a fuel used mainly to power spark ignition engines. It can also act as a solvent (e.g. petroleum ether). Gasoline consists mainly of aliphatic hydrocarbons, it also contains certain amounts of aromatic and unsaturated hydrocarbons. The most important properties of gasoline are: the octane number (i.e. resistance to detonation), the ability to form combustible mixtures, and the tendency to form resin deposits. There are several types of gasoline:
a) Lead gasoline – Ethyl. It was used until the mid-1980s. It contained a tetraethyl lead which, when burned in the engine, led to the formation of toxic lead oxides.
b) Unleaded petrol (95 RON) – cheaper type of unleaded petrol, with octane number 95.
c) Unleaded petrol (98 RON) – the more expensive variant, with the octane number 98.
In order for gasoline to become a commercial product, it is also necessary to include in its composition a number of additives that prevent adverse and undesirable phenomena during storage, use and transport of fuel.
Petrol additives
The most important gasoline additives include oxidation inhibitors. Due to the fact that gasoline as a product is a mixture of hydrocarbons, it may undergo oxidation during storage. This leads to deterioration of the fuel’s properties by lowering its octane number. Typically, the oxidation inhibitors include aromatic amines and phenols.
The second group of additional substances are metal deactivators. They support oxidation inhibitors by counteracting the catalytic effect of metals on the reactions of petrol oxidation. Their operation consists of creating protective layers on the surface of metals.
Essential additions are also dispersing-emulsifying compounds that keep sediments and corrosion products in the dispersion state. The product group that can perform such functions are ROKAmers. These products belong to the group of non-ionic block copolymers of ethylene oxide and propylene. This feature distinguishes the ROKAmer group from other non-ionic surfactants and determines their anti-foaming properties.
Another group of additives are lubricants. They prevent fast wear of fuel pump components that require proper lubrication. Examples of such compounds may be carboxylic acids, esters or amines. Water from gasoline is removed using de-emulsifiers, thanks to which it is released as a separate phase in the tank. This is especially important when, for example, pumping fuel. In order to counteract this phenomenon, the above mentioned additives called de-emulsifiers are used.
Most installations in the oil industry are made of steel, and therefore corrosion may occur in the presence of water, resulting in a risk of leakage. Corrosion inhibitors are used to prevent this. They react with the surface of the metal, creating a protective barrier, thus preventing the influence of corrosive agents. Usually, these are compounds based on amines, amides or ammonium salts.
The last, but no less important feature of modern motor gasolines is their ability to keep the fuel system (in particular the intake system) and engine combustion chambers clean. For this purpose, refining additives called detergents are used. The product of PCC Group, Petrotex DF30, will work perfectly for this purpose. It is a yellow, oily liquid used as an ingredient in dispersing and emulsifying compositions. The most important feature of this product is its washing capability. Petrotex DF30 is mainly used as a detergent to clean the inlet and outlet valves of cylinders. Dodecylphenol is also perfectly suited as an additive to the fuel system cleaning agents. It is a thick, viscous liquid with a yellow colour and a phenolic odour. Dodecylphenol is used for the production of propoxylates that form synthetic components of fuel additive packages.
Liquid fuels – diesel oil
Diesel fuel is a fuel intended mainly for diesel engines with self-ignition. It is a mixture of paraffin, naphthalene and aromatic hydrocarbons separated from petroleum in distillation processes. It is a petroleum fraction boiling at 180-350oC. The most important parameters of this liquid fuel are: viscosity (spraying), resistance to self-ignition (cetane number) and the temperature of solidification, as well as the sulfur content. Due to the fact that distillates of diesel oil have a high content of sulfur compounds, it is necessary to remove them through hydrotreating.
Additives for diesel oil
Diesel oil in current use requires the use of various enriching additives. Most of them perform similar functions to those intended for gasoline. The key in the case of diesel, however, is the use of anti-foam additives, anti-electrostatic additives and modifiers increasing the cetane number.
Anti-foaming agents are designed to prevent the formation of foam during fuel preparation and filling of tanks. Some diesel fuels also tend to foam during pumping, which disrupts the process of filling the tank, causing leaks. The ROKAmer series products prevent this. These are anti-foaming agents that can be used in a very wide range of temperatures. In addition, ROKAmers are characterized by very good degreasing properties and the ability to reduce the surface tension between liquid and air. In this way they improve foam drainage, resulting in its reduction.
Antistatic additives are designed to increase the electrical conductivity of diesel oil, thereby reducing the risk of fire. Typically, for this purpose, copolymers of olefins and acrylonitrile in combination with polyamines are used.
Another group of modifiers are additives that increase the cetane number. Their task is to shorten the ignition delay time and increase the burning rate. The most popular of them are 2-ethylhexyl nitrate (EHN) and di-tert-butyl peroxide (DTBP).
An important group of additions are also markers. Their role is to facilitate the identification of the type of fuel. In order to distinguish fuel oil from heating oil, azo derivatives are introduced which colour the fuel to a given colour. Recently, fragrance additives have become very popular, which are used where the smell of oil or gasoline is troublesome. Such modifiers can be for example esters or terpenes.
Liquid fuels – kerosene
Kerosene is a fuel used in very large quantities, mainly in aviation for turboprop or jet engines. It is also used as a solvent and ingredient in cosmetic formulations. Due to the fact that it has a low octane and cetane number, it cannot be used in spark-ignition engines (gasoline engines) as well as in self-propelled engines (Diesel engines). Kerosene is a liquid petroleum fraction boiling at about 170-250oC. Its production is relatively cheap. Kerosene is formed mainly in the process of crude oil rectification. Usually, additives and refinement processes, such as those for the production of gasoline and diesel oil, are not used for this type of fuel. Kerosene is also converted to gasoline, as well as other products in the processes of cracking and reforming.
Liquid fuels – biodiesel
Biodiesel is a renewable alternative for oil-derived diesel. It is obtained from vegetable or animal oils. Biodiesel usually contains pure methyl esters of fatty acids or ethyl esters of fatty acids. Often fuel blends with diesel oil are also called biodiesel. They are used to obtain fuel that ensures better engine operating conditions. Pure biodiesel adversely affects rubber hoses and fuel lines. In addition, its viscosity varies greatly when the temperature rises, which may require the use of an additional cooler for biodiesel. Another disadvantage of this fuel is its precipitation at low temperature, which causes clogging of filters and other engine components during operation in winter conditions. Of course, biodiesel also has a number of advantages. First of all, it does not poison the air with sulfur compounds, it is biodegradable, it does not increase the CO2 concentration in the atmosphere, and its production allows wastelands to be made use of.
Biodiesel additives
High-quality multifunctional diesel additives reduce many of the problems associated with biodiesel blends, such as fuel system corrosion, water separation and increased foaming of fuel. For this purpose, very similar modifiers as those added to diesel oils are used. The key and often concerning issue of the use of biodiesel is its impact on the cleanliness of injectors and the possibility of serious coking, as well as contamination of nozzles. For this purpose, agents known as dispersants are used. The PCC Group offers ROKAcet series products that can act as dispersants. ROKAcets are general purpose agents that can be successfully used in a variety of industrial applications.
Mixing biodiesel with conventional diesel fuels can further aggravate its foaming properties. This is particularly troublesome when, for example, filling the fuel tank at a gas station. To prevent this phenomenon, anti-foam additives are used. The above-mentioned products of the ROKAmer series are perfect for this role.