Paints are substances that have the task of creating protective or decorative coatings on the surface of various objects. They are usually in liquid form.
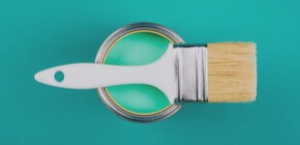
Paints and coatings
The basic components of paints are:
a) binders and film-forming substances – these are ingredients that are found in all types of paints, varnishes and emulsions. They create a thin film-forming coating on the surface of the painted element and are designed to give the paint appropriate properties such as gloss, durability, adhesion, resistance to weather conditions, strength and flexibility. Substances that can act as binders in paints are synthetic or natural resins, such as, polyurethanes, polyesters, vinyl acetate/ethylene (VAE), silanes, epoxy resins or oils,
b) thinners – they are used to dissolve the polymer and reduce the viscosity of the binder. They are characterized by high volatility, thanks to which they evaporate easily when drying and do not become part of the paint. An additional task for thinners is to control flow properties and applications. They can also affect the stability of liquid paint. The main diluent for water-borne paints is, as the name suggests, water. Oil paints (otherwise known as solvent) usually contain combinations of various organic solvents, such as aromatic compounds (toluene or other xylene derivatives), alcohols or ketones. The PCC Group has in its offer Dichloropropane, which can successfully replace organic solvents such as toluene, xylene and acetone. Dichloropropane is a highly effective solvent for resins, greases and fats, therefore it is used as a base component in the remover of varnish coatings drying at ambient temperature. Due to its chemical properties, it can also be successfully used in the production of paints and varnishes, as well as printing inks,
c) pigments – designed to give the paint the right colour. They appear in the form of granular solids. They can be divided into natural or synthetic pigments. The most popular natural pigments are various clays, silicas, calcium carbonate and talcs, whereas among synthetics there are calcined clays, barium sulphate (so-called blanc fixe), precipitated calcium carbonate or pyrogenic silicas. A special type of pigment are fillers. These are granular solids, which are designed to increase the volume of paint, strengthen its structure, or reduce the cost of paint production, due to the fact that they are relatively cheap. Examples of widely used paint fillers are diatomaceous earth, talc, lime, barite and clay,
d) modifying additives – these are ingredients added in small quantities that modify the properties of paints. They can, among others, change the surface tension, improve flow properties and pigment stability, control foaming, prevent freezing. The PCC Group in its offer has a number of modifying additives that significantly improve the quality of the obtained coatings. The products ROKAdis 900 and ROKAdis 905 are perfectly suited as dispersing and wetting additives. They also reduce the viscosity of the formulation and provide very good stabilization of inorganic pigment concentrates. The ROKAdis product range, included in the PCC Group’s offer, ensures very high efficiency at very low concentrations in the formulation (1-5%). On the other hand, EXOdis PC950, in addition to its dispersing properties, can also be used as a non-ionic wetting agent in the manufacture of paints. Due to the fact that EXOdis PC950 does not contain alkylphenols and volatile organic compounds (VOC), it can be a component of modern and ecological paints and coatings. On the contrary, ROKAnol K14 can be used as a dispersant of dyes and pigments. In addition, it is also used as a latex dispersing agent in dye formulations.
Another very important group of additives for paints and coatings are emulsifiers. They help to create a permanent, uniform emulsion, which directly translates into easier application of paint on any surface. The PCC Group offers a wide range of emulsifiers that can act as additives in the production of paints, e.g. products from the ROKAnol or ROKwin series. Particularly noteworthy are the POLIkols , which can be characterized by a wide range of application uses. Due to their structure, polyoxyethylene glycols have very good softening and solubilizing properties, low viscosity and freezing point as well as very good solubility in the aqueous environment. Due to its high hydrophilicity and specific construction ROKAmer 1010/50 can also be characterized by very good emulsifying abilities. Emulsion products made with its use can be used in the paint and varnish industry.
Paints – their types and application
In general, paints can be divided depending on their properties and application:
a) emulsion paints, also known as dispersion paints. They can be divided depending on the type of adhesive used:
● acrylic paints – their binder is water dispersion of acrylic resin. They are characterized by very good flexibility and adhesion to the substrate. Acrylic paints have a wide range of applications and can be used to cover, for example, wood, concrete, plastics, plasters and many other surfaces. They have high abrasion resistance and allow water vapor, however, the surfaces painted are susceptible to various types of damage,
● latex paints – the binder of this type of paint is rubber. Latex paints are extremely resistant to moisture and cleaning. Their advantage is a very easy application on various surfaces. The disadvantage is usually the high price. An example of the most modern latex paints are ceramic paints. They contain ceramic particles that form the so-called stain resistant coating. Thanks to this, the walls painted with them do not absorb dirt and dust,
● acrylic-latex paints – have the characteristics of acrylic paints, i.e. good air permeability and scrub resistance, and flexibility of latex paints,
● Vinyl paints – the binder of these paints is polyvinyl acetate or polyvinyl chloride. They are used mainly in utility rooms, and their greatest advantage is easy washability. Unfortunately, they also make it difficult for the walls to breathe due to the low vapor permeability.
b) lime paint – the binder of these paints is lime putty diluted with water. They are cheap, but not durable. In order to increase the durability, admixtures of other water-borne adhesives (e.g. glue) or the addition of polyvinyl acetate are used. Lime paints are used for painting fresh concrete substrates, lime plasters and walls previously painted with lime paints. Currently, the use of these paints is very rare. This is due to their very low durability, dustiness and tendency to create cracks,
c) distempers – these are durable and breathable paints with excellent solubility in water. Plant or animal glues are their binder. Distempers are not very resistant to dirt, they cannot be washed and they absorb moisture from the environment. They are mainly suitable for painting lime and cement-lime plasters. Distempers are practically no longer used because they have been replaced by more modern paints,
d) silicate paints – their binder is potassium water glass. These paints are durable, non-flammable, resistant to moisture and have high mechanical resistance. They can be applied on brick, concrete and wooden substrates. When drying, they cure under the influence of CO2 contained in the air,
e) silicone paints – create a durable and weather-resistant coating. They are produced based on a silicone resin. They are suitable for painting concrete, wooden, brick and plaster substrates. These paints have the ability to self-clean,
f) epoxy paints – these are two-component paints, consisting of an epoxy resin and a hardener. Before applying, both components are mixed together. Epoxy paints show high resistance to mechanical damage and chemicals. They are used, for example, for painting concrete floors. For their production, additives based on phosphate esters from the Roflam series (F5, B7, P) can be used. These products provide high fire resistance to the materials to which they are added. Thanks to that, they can be used in passive fire protection systems, recommended in the protection of steel structural elements against the effects of hydrocarbon and jet fire. The products of the Roflam series can be used as components while creating formulations of intumescent paints, that are used on a large scale in public places (e.g. airports, halls, car parks, etc.). In addition, Roflam products have also very wide usage in the petrochemical, energy, oil and gas industries,
g) chlorinated rubber-based paints – a binder for this type of paint is obtained by chlorination of the rubber with addition of softening agents. Chlorinated rubber-based paints formed in this way are resistant to water, acids and alkalis, but are very sensitive to all organic solvents (except alcohol). They can be used as protective paints for gates and fences,
h) vinyl paints – they are resistant to water and various chemical compounds. Polyvinyl chloride is most often used as a binder. Vinyl paints are mainly used as coatings for materials made of galvanized steel, such as gutters and window sills,
i) polyurethane paints – are produced based on polyurethane resins. There are two types of these paints: one and two components. One-component paints are cured under the influence of moisture, while two-component paints require the addition of a hardener. Polyurethane paints create hard and abrasion-resistant coatings. They are used for painting wooden, metal and plastic surfaces. They are characterized by very high toxicity,
j) structural paints – this is a special type of paint that is applied to the surface with a thick layer, and then after drying it gives them a suitable pattern (structure). Thanks to these types of paints, you are able to achieve a variety of decorative wall textures. Structural paints are suitable for covering concrete, wooden, gypsum plasterboards, plasters and many others,
k) spray and powder paints – they are used to obtain special visual effects on surfaces. They are applied to various surfaces using a gun. Thanks to these types of paints, it is possible to obtain coatings resistant to all kinds of cracks and splinters. Products of the PCC Group from the Rostabil series (TNF, TPP, DPDP, DDPP) can be successfully used for the production of powder coatings in thermal processing. It is a group of antioxidants with a structure based on organic phosphates. Products from the Rostabil series can also be used as effective thermal and processing stabilizers. Thanks to their unique properties, they provide colour control during machining and curing cycles.
Varnishes – their types and description
Paints known as varnishes contain a solid binder dissolved in a solvent and are dried out as a result of its evaporation. They are widely used as materials for covering surfaces for decorative and protective purposes.
Varnishes also have the ability to quickly cure in a very wide temperature range. Varnish is a type of finish that can create transparent or pigmented coatings, where the main raw material is a hard and linear polymer. The nature and properties of varnishes are strongly dependent on the type of their structure. The most popular solvents for the production of varnishes are usually white spirits or mineral turpentine. It is possible to distinguish many types of varnishes, which can be generally divided into two groups: solvent-based and water-based.
Types of solvent-based varnishes
Solvent-based varnishes form very hard coatings that show high resistance to mechanical damage. By creating a homogeneous structure, they also prevent the penetration of moisture. The most important component of this type of varnish is the solvent, which is usually characterized by an unpleasant and intense smell. Solvent-based varnishes can be divided into a number of subgroups:
a) solvent-based polyurethane varnishes – they are one of the best varnishes available on the market. There are one- and two-component varnishes. One-component polyurethane varnishes use the moisture contained in the air to harden. In contrast, the characteristic feature of varnishes based on two components are two stages of drying. During the first stage, the solvent evaporates, then the chemical drying takes place and the varnish is hardened. The advantages of polyurethane varnishes are their resistance to moisture, as well as high flexibility. Unfortunately, they are usually very toxic. They allow to obtain a wide range of finishes, from satin to gloss. Polyurethane varnishes, due to their abrasion resistance, are mainly used for varnishing floors in rooms with high intensity of movement, such as halls and lounges,
b) nitrocellulose lacquers – the main raw material for their production is nitrocellulose resin. It is usually obtained from cotton, which is treated with sulfuric or nitric acid. The nitrocellulose varnishes also contain a number of other substances, such as polyester and alkyd resins, which improve their hardness and gloss. Plastifying additives are also used, most often phthalates, which increase resistance to light and temperature. Nitrocellulose varnishes are used as materials for painting furniture and various wooden elements. They are also used as a base layer for polyurethane varnishes,
c) oil-resin varnishes – raw materials used for their production are drying oils, natural or synthetic resins, thinners and usually a large number of additives modifying their appearance or properties. These varnishes are characterized by high resistance to atmospheric factors, in particular to UV radiation. Unfortunately, they also show poor hardness and abrasion resistance. They can be used for painting all wooden surfaces, from panelling to windows and doors. They can also be used as floor coatings in rooms with low traffic,
d) spirits varnishes – they have a very short drying time, which usually does not exceed 60 minutes. Unfortunately, they are not resistant to all impacts and atmospheric conditions. Raw materials for the production of spirits varnishes are solutions of natural or synthetic resins dissolved in ethyl alcohol. Spirit varnishes can be used to paint toys and various wooden elements in interiors. An example of a widely used varnish of this type is polish, which gives a relatively hard coating with a characteristic gloss.
Water-based varnishes – types and applications
In the case of waterborne varnish, the main diluent is water. The methyl ester is responsible for their flexibility and surfactants are substances that reduce their surface tension. The PCC Group offers a wide range of different surfactants that can be used in the paint and varnish industry. EXOdis PC30 can be used as a basic dispersing agent in water-soluble formulations. Due to its structure (aqueous polyacrylic acid), water-based varnishes achieve excellent final stabilization. This product can also be used for the production of white decorative paint for interiors.
Water-borne varnishes can be divided into three groups based on the type of adhesive used:
a) acrylic varnishes – these are cheap substances that create transparent coatings, without changing the colour of the wood. They are characterized by low abrasiveness and mechanical resistance and their biggest advantage is low toxicity. They are mainly used for painting wooden household products and painting floors in places with low traffic,
b) water-based polyurethane varnishes – they show very high resistance to abrasion and mechanical damage. In addition, they are insensitive to moisture and temperature changes. Like polyurethane solvent-based varnishes, they are divided into one- and two-component varnishes. Due to the creation of very durable coatings, they are often used on floors in living rooms,
c) polyurethane-acrylic varnishes – their properties depend on the proportion of both components. Varnishes containing more polyurethane in composition are characterized by higher hardness. Polyurethane-acrylic varnishes exist in one or two-component form. They can also contain a number of hardeners that improve their mechanical strength and abrasion resistance. Unfortunately, it also increases their toxicity.
Modern waterborne paints contain a variety of different components. Therefore, it is particularly important to mix them thoroughly in order to ensure proper consistency and stability of the paint. Exactly for this purpose dispersing agents are used. In addition to providing the appropriate performance properties of the paint, they also give it the desired colour saturation and ensure adequate pigmentation. Rodys series products are highly effective dispersants used in paints containing water as a solvent. Ideally suited for aqueous dispersions of dyes, organic and inorganic pigments as well as reinforcing pigments. Optimum results can be observed when using pigment pastes based on iron oxides. Thanks to the effective prevention of agglomeration of pigment particles, the final product is perfectly coloured. In addition, Rodys series products reduce the viscosity of suspensions in dispersions with high solids content. This range of products is used for the processes of varnishing textiles, rubber, bitumen and concrete. Another dispersing agent that provides excellent stabilization of white waterborne paints is Tensol DDM. It has very good dispersing properties against titanium white and mineral fillers. Thanks to the usage of Tensol DDM, high compatibility of pigments in paint products is obtained.