The rubber industry represents an important role in the global industry. The production and processing of rubber in its various forms is used in many areas, including the manufacture of tyres, automotive parts, industrial goods, technical articles and consumer products. The varying properties of rubber determine their various functionalities tailored to manufacturers' requirements.
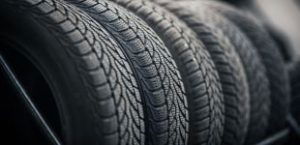
Rubber is the product of a vulcanisation process that uses natural rubber, artificial rubber or a mixture of the two. The formulation generally consists of approximately 3% sulphur incorporated together with various process additives. Rubber as a material is characterised by its high elasticity, as well as its considerable resistance to the harmful effects of chemical agents.
Natural rubber
The main raw material for rubber is natural rubber, which is structurally a cis-1,4 polyisoprene. It is found in many plants in the form of latex, a colloidal system in which the dispersed phase is mainly natural rubber and the dispersion medium is water. In addition to these components, latex also contains fatty acids, lipids, carbohydrates and minerals. Latexes from different sources vary in composition and content of individual components. The largest producers of latex are Thailand, Indonesia and Malaysia and India. Natural latex is obtained from the pressed milk sap of rubber plants. Synthetic latex can be an intermediate or an end product in the production of synthetic rubbers.
Synthetic rubbers
This group includes all rubbers obtained by chemical synthesis. World production of synthetic rubbers is comparable in volume to natural rubber. Synthetic methods mainly use emulsion and solution polymerisation. The most popular of the synthetic elastomers are:
General purpose:
- Styrene-butadiene rubber (SBR)
- Ethylene propylene diene rubber (EPDM)
- Isoprene rubber (IR)
- Butadiene rubber (BR)
Special purpose:
- Chloroprene rubber (CR)
- nitrile(-butadiene) rubber, (NBR)
- Butyl rubber (IIR)
Specific purpose:
- Fluorosilicone (FVMQ)
- Fluorocarbon and derivatives (FKM)
- Hydrogenated nitrile (HNBR)
Rubber industry
The rubber industry involves the production of various types of products, with tyres and tubes accounting for the largest share – around 60% of global production. Of this, 60% is accounted for by passenger car and light truck tyres and around 26% by truck tyres. Other applications include: rubber hoses, conveyor belts, footwear, technical articles, soaked goods (disposable gloves), textiles with a rubber backing and adhesives.
The properties of the rubber depend on the type and amount of components used in the rubber compound. By appropriately selecting the components of the rubber compound, rubber with different physical and chemical properties can be obtained. The selection of the components of the mixture is carried out in order to obtain a finished product with the appropriate characteristics, which include:
- abrasion resistance (tyre rubber);
- high-temperature resistance;
- low-temperature resistance;
- flame retardation;
- properties required for materials used in the food industry, medicine, etc.
Rubber compound components
In addition to rubber or a mixture of several rubbers, the rubber compound consists of the following components.
- Fillers – significantly increase the rubber’s resistance to abrasion or improve its resistance to chemicals. Active fillers have a particular role to play in the case of synthetic rubbers, as rubber products derived from this type of rubber are in practice unusable. The reason is the very low mechanical strength compared to natural rubber. The most common filler in the rubber industry is carbon black, which is the product of incomplete combustion of oil or gas, combined with thermal decomposition and the release of carbon. Active and semi-active carbon blacks are the most commonly used. High Abrasion Furnace and Intermediate Super Abrasion Furnace types have a very high abrasion resistance and prevent heat build-up in the tyres – they are active carbon blacks. Semi-active types include: Fast Extrusion Furnace and General Purpose Furnace types of carbon black for rapid extrusion and for general applications. An equally important filler in the design of rubber compounds is silica. As with carbon black, it significantly increases the abrasion resistance of the rubber. However, it has properties, i.e.: formation of permanent particle agglomerates, difficulty in framing into non-polar rubbers, strong adsorption of particles of accelerators of the vulcanising system. It is therefore necessary to use activators (Polyglycols) and coupling agents together with silica. The PCC Group has a range of polyoxyethylene glycols (PEGs) dedicated to the rubber industry under the trade name Polikol. Dedicated products include Polikol 1500 Flakes, Polikol 4500 Flakes, Polikol 6000 Flakes and Polikol 8000 Flakes. Products can come in flake form, but also in powder or pastille form.
- Plasticisers – ensure adequate runnability of the rubber compound to facilitate processing. They also affect the mechanical properties of unvulcanised and vulcanised compounds. Depending on the type of rubber, plasticisers of synthetic origin (phthalates, terephthalates,) and those obtained from crude oil processing (mineral oils: paraffinic, naphthenic, aromatic) are used. The PCC Group has a range of specialised plasticisers in the Roflex series with a flame retardant function. Among the most effective in fire response are Roflex 50 / Roflex 65 and Roflex T70. Plasticisation at low temperatures is effectively provided by Roflex T45. For specialised formulations with higher viscosity and for human and environmentally sensitive applications, Roflex T70L is dedicated. The plasticisers in the Roflex range act synergistically with conventional plasticisers to provide excellent mechanical properties to the finished product.
- Flame retardants – chemicals that reduce the flammability of rubber products. Among the most important are aluminium and magnesium hydroxides, antimony trioxide, chloroparaffin and ammonium polyphosphate. The use of such additives together with the Roflex range of flame retardant plasticisers offers the possibility of a synergistic effect to improve the flammability profile of rubber products.
- Cross-linking system – all additives that are designed to change the structure of the rubber due to the formation of bridges between the rubber chains. Cross-linking with sulphur (vulcanisation) or metal oxides and peroxides is the most common. Elemental or polymeric sulphur is used, and as activators, e.g. zinc oxide together with stearin. The use of accelerators is important: dithiocarbamates, thirams, thiazoles or thioureas.
- Other additives – this is a huge group of additives that alter the specific properties of rubber compounds. Antioxidants, anti-ozonants, protective waxes or dyes and pigments are used. Among the group of antioxidants, thermal stabilisers can be distinguished, which are used for mixtures that tend to decompose at processing temperatures. The PCC Group’s product range includes a number of such products – the Rostabil series. These additives have antioxidant properties and can also act as thermal stabilisers, preventing the degradation of rubber compounds during processing.
A very interesting group of additives are those that provide antistatic properties by lowering the surface resistance of the finished product. The PCC Group offers liquid antistatic agents under the trade name EXOstat. When introduced internally, this additive migrates to the surface of the product, where it interacts with atmospheric moisture, reducing the surface resistivity and allowing the static charge to dissipate over a long period of time.