Korozja materiałów jest powszechnym zjawiskiem, którego nie da się zupełnie wyeliminować. Niszczenie korozyjne często jest zaliczane do głównych przyczyn strat materiałowych. Ponadto przyczynia się do zanieczyszczenia środowiska oraz stwarza zagrożenie dla zdrowia ludzkiego. Poznanie mechanizmów korozyjnych oraz sposobów ochrony przed degradacją materiałów pozwala w znaczny sposób zabezpieczać materiały.
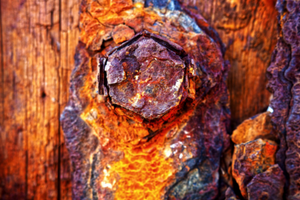
Co to jest korozja?
Przedmioty użytkowe czy elementy architektury wykonane z metali oraz ich stopów, codziennie poddawane są narażeniu na różnorodne czynniki środowiskowe. Na skutek tego dochodzi do niszczenia materiałów w wyniku chemicznej lub elektrochemicznej reakcji, która określana jest jako korozja (odpowiednio chemiczna lub elektrochemiczna).
Korozja często jest nazywana rdzewieniem – określenie to dotyczy materiałów metalowych. Na ich powierzchni pojawia się wtedy charakterystyczny, rudy nalot, czyli rdza. Rdza nie jest pojedynczym związkiem chemicznym, a warstwą tlenków, wodorotlenków oraz soli żelaza (produkty utleniania żelaza oraz jego stopów, np. stali).
Czynniki środowiskowe, pod wpływem których zachodzi korozja:
- opady atmosferyczne,
- wilgotność,
- zanieczyszczenia środowiska (np. tlenki siarki, tlenki azotu, kurz),
- nieodpowiednie pH,
- naprężenia materiałów,
- obecność bioorganizmów,
- kontakt z glebą.
Korozja chemiczna i elektrochemiczna
Korozja chemiczna
Korozja chemiczna zachodzi w środowisku, gdzie brak jest przewodności jonowej, czyli najczęściej w obecności gazów spalinowych, ropy naftowej, wybranych substancji organicznych czy gazów takich jak wodór, siarkowodór, tlenek węgla (II), a także chlor. Korozję chemiczną czasami nazywa się także korozją suchą. Materiał ulegający korozji zazwyczaj styka się całą powierzchnią z czynnikiem korodującym. Ale na ogół nie stanowi dużego zagrożenia dla konstrukcji.
Korozja elektrochemiczna
Zachodzi w środowisku zdolnym do przewodzenia ładunków elektrycznych (w elektrolitach). Takim środowiskiem może być np. woda wraz z rozpuszczonymi gazami oraz solami. Dochodzi wtedy do utworzenia na powierzchni materiału lokalnych ogniw galwanicznych (np. miejsce zetknięcia z wilgocią). Obecność elektrolitu powoduje zamknięcie obwodu. Skutkiem korozji elektrochemicznej jest utlenienie się powierzchni metali i powstanie brunatnego osadu, czyli rdzy.
Korozja metali, a ich pasywacja
Powierzchnia metalu stykająca się z czynnikiem korodującym, pod jego wpływem ulega utlenieniu – na powierzchni tworzy się warstwa tlenku metalu. Nie zawsze jest to zjawisko niepożądane. Pasywacja jest zjawiskiem, podczas którego tworzy się dostatecznie zwarta i silnie związana z powierzchnią metalu warstwa tlenku. Jej zadaniem jest ochrona przed dalszą degradacją materiału (dalszym utlenianiem).
Zjawisko pasywacji zaobserwować można np. w przypadku glinu. Pomimo, że jest to metal o dużej reaktywności, to wykazuje odporność na korozję, właśnie dzięki pasywacji. Metale powszechnie poddaje się procesom pasywacji – jest to jedna z technik antykorozyjnych. Istnieje także naturalna pasywacja. Można ją zaobserwować dla miedzi, na której powierzchni tworzy się zielony nalot nazywany patyną.
Czy tylko metale ulegają korozji?
Na elementach metalowych oraz wykonanych ze stopów metali, najczęściej obserwuje się degradację pod wpływem korozji chemicznej bądź elektrochemicznej. Korozja elektrochemiczna żelaza, stali, miedzi czy aluminium jest powszechna, ale to zjawisko dotyka również inne materiały, nie tylko metaliczne, np. mamy do czynienia z korozją chemiczną betonu.
Materiały ulegające korozji (inne niż metale):
- beton i żelbet,
- tworzywa sztuczne,
- drewno,
- ceramika.
Dla poszczególnych materiałów, mechanizm korozji jest odmienny. W dużej mierze zależy ona od typu przewodności elektrycznej na granicy faz materiał-środowisko. Ponadto istotną kwestią jest rodzaj środowiska, w którym przebywa materiał. W przypadku ciał charakteryzujących się dużą przewodnością, do czynienia mamy zazwyczaj z korozją elektrochemiczną. Natomiast przy niskiej przewodności (lub jej braku), charakter korozji jest zdecydowanie bardziej chemiczny (lub fizykochemiczny).
Techniki antykorozyjne
Zjawiska korozji nie można całkowicie wyeliminować. Wszelkie techniki antykorozyjne mają na celu spowolnienie tego procesu. Metale szlachetne, które występują naturalnie w postaci niezwiązanej, nie wymagają ochrony antykorozyjnej. Są to na przykład złoto czy platyna.
Sposoby ochrony przed korozją:
- wyeliminowanie czynników odpowiedzialnych za procesy korozyjne ze środowiska, np. eliminacja wilgoci, stosowanie wymieniaczy jonowych w celu usunięcia rozpuszczonych w wodzie soli, zobojętnianie substancji o odczynie kwaśnym;
- stosowanie substancji zmniejszających szybkość korozji (inhibitorów);
- zmiana potencjału elektrodowego metalu;
- stosowanie powłok ochronnych. Metal można pokryć innym, bardziej szlachetnym metalem od metalu chronionego – powłoka izolująca, lub mniej szlachetnym metalem – powłoka ekranująca;
- stosowanie powłok nieorganicznych, np. emalie szkliste, powłoki chromianowe;
- stosowanie powłok organicznych, np. tworzywa polimerowe, farby nawierzchniowe.
Popularną ochroną antykorozyjną jest stosowanie powłok. Nakładane są one poprzez zanurzenie elementu w stopionym metalu (pokrywanie ogniowe) lub nanoszone są z wodnego roztworu elektrolitu, przez elektrolizę (pokrywanie elektrolityczne). Mniej popularna metoda nakładania powłoki to metalizacja natryskowa, czyli wykonana przy użyciu pistoletu.
Najczęściej stosowanym metalem ochronnym jest cynk. Wykorzystywany jest szczególnie jako powłoki na stali czy żeliwie. Powłoka cynkowa wykazuje dobre właściwości ochronne, pomimo niższej termodynamicznej stabilności w porównaniu do żelaza. Sama chroniąc element metalowy przed degradacją, w kontakcie z wilgocią również może ulegać procesom korozyjnym. Wytrzymałość powłoki cynkowej zależy nie tylko od jej grubości, ale także od warunków środowiskowych, w których użytkowany jest dany element. Ze względu na sposób nakładania, wyróżnia się cynkowanie galwaniczne oraz cynkowanie ogniowe.
Ekonomiczne skutki korozji w skali globalnej
Korozja jest światowym problemem. Nadal są odnotowywane ofiary śmiertelne, straty gospodarcze oraz skutki środowiskowe spowodowane korodowaniem materiałów. Korozja może doprowadzić do poważnych awarii w zbiornikach ciśnieniowych, częściach samolotów czy urządzeniach trakcyjnych.
Jak podaje Mohmmad A Jafar Mazumder w artykule „Global Impact of Corrosion: Occurrence, Cost and Mitigation (2020)”, typowe koszty utrzymania związane z problemami korozyjnymi dla danego kraju wahają się od 1 – 5% jego produktu krajowego brutto. W 2013 roku organizacja NACE International przeprowadziła globalne badanie na temat ekonomicznych skutków korozji. Miały one m. in. na celu pokazanie jak istotne jest zintegrowanie technologii antykorozyjnej z systemami zarządzania. W opublikowanym raporcie określono koszty korozji na 2,5 biliona $, czyli 3,4% PKB, co oznacza, że corocznie kraje na całym świecie, w budżetach muszą uwzględnić znaczne sumy na walkę z procesem korozji.
Źródła:
https://irispublishers.com/gjes/fulltext/global-impact-of-corrosion-occurrence-cost-and-mitigation.ID.000618.php
https://psk.org.pl/aktualnosci/ekonomiczne-skutki-korozji