Przemysł włókienniczy jest często nazywany jednym z najdłuższych i najbardziej skomplikowanych łańcuchów przemysłowych. W jego skład wchodzi duża liczba podsektorów, które swoim obszarem obejmują cały cykl produkcyjny, zaczynając od produkcji surowców (np. włókien sztucznych), poprzez półprodukty (np. przędza i tkaniny), aż do produktów końcowych, takich jak dywany, odzież i wyroby włókiennicze do użytku przemysłowego.
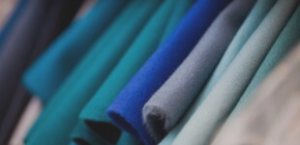
Dziś ciężko wyobrazić sobie świat pozbawiony tekstyliów. Dotyczy to zwłaszcza odzieży, którą każdy z nas nosi na co dzień. Ubrania zapewniają wygodę i ochronę, a dla sporej grupy osób stanowią także niezwykle ważny wyraz stylu i osobowości. Sektor tekstylny jest branżą niesamowicie rozdrobnioną i niejednorodną. Sprawia to, że jest zdominowany głównie przez małe i średnie przedsiębiorstwa. Skupia on w sobie trzy istotne rodzaje wyrobów finalnego przeznaczenia: odzież, wyposażenie mieszkań oraz zastosowania przemysłowe.
Włókna tekstylne wytwarzane są z ogromnej ilości materiałów. Większość z nich charakteryzuje się budową polimeryczną. Głównymi surowcami do produkcji włókien są:
- włókna naturalne – są to włókna zwierzęce (inaczej białkowe – np. jedwab, wełna, włosy), roślinne (celulozowe – np. len, konopie, bawełna, pokrzywa) lub mineralne, występujące w wielu naturalnych minerałach,
- włókna sztuczne – wytwarzane przez człowieka. Mogą to być włókna oparte na celulozie (np. octan celulozy) lub też na syntetycznych polimerach np. nylon, włókna poliakrylonitrylowe (anilana), poliestrowe (elana) i poliuretanowe (lycra),
- materiały z recyklingu (tzw. rPET) – są to materiały pochodzące z odnawialnych surowców naturalnych, np. PLA (Polilaktyd), który produkowany jest głównie z kukurydzy i ulega biodegradacji, czy też włókna cupro, powstałe w wyniku wytrącania się włókien celulozowych w kąpieli miedzianej.
Pierwszym procesem przetwórczym, jakiemu poddawane są włókna naturalne oraz sztuczne, jest przędzenie. Początkowo luźne włókna przechodzą przez szereg różnych operacji mechanicznych (rozluźnianie, mieszanie i zgrzeblenie), a następnie poddawane są przędzeniu właściwemu. Proces ten możemy podzielić na dwa podstawowe rodzaje:
- wełniarski – stosowany jest do otrzymywania przędz z włókien naturalnych (wełny) oraz przędz mieszankowych, które zawierają wełnę oraz włókna syntetyczne, np. poliestrowe, poliakrylonitrylowe lub poliamidowe,
- bawełniarski – stosowany jest do otrzymywania przędz bawełnianych oraz mieszanych, w skład których wchodzą włókna bawełny oraz innych materiałów, włókna poliestrowe, wiskozowe lub poliamidowe.
W procesie przędzenia stosowane są trudnodegradowalne związki chemiczne, które nanosi się na włókna w ilości od 2 do 5% substancji masowych. Służy to ułatwieniu przebiegu kolejnych etapów procesu wytwarzania przędzy. Najczęściej stosowane są tutaj oleje mineralne i silikonowe oraz węglowodory aromatyczne, które na etapie obróbki końcowej zostają całkowicie usunięte z przędzy. Wytwarzane są z niej dwa podstawowe asortymenty płaskich wyrobów włókienniczych, czyli tkaniny i dzianiny.
W przypadku tkanin pierwszą operacją wstępną jest klejenie osnów. Polega ono na aplikacji specjalnych substancji chemicznych na przędzę, co zwiększa jej wytrzymałość mechaniczną. W tym celu stosowane są tzw. klejonki. Mogą być one oparte na bazie polisacharydów (np. karboksymetyloceluloza) lub polimerów syntetycznych, takich jak poliakrylany. Inaczej jest w przypadku procesu wytwarzania dzianin. Przędza do ich produkcji jest specjalnie przygotowywana poprzez naniesienie preparacji poślizgowych. Substancje te mają na celu zmniejszenia naprężeń w procesie dziania, które wynikają z powstającego tarcia między przędzą a elementami prowadzącymi maszyny.
Jako przykład preparatu stosowanego na etapie klejenia może posłużyć produkt o nazwie Rokrysol JW20, który jest efektywną, syntetyczną klejonką. Nadaje klejonej przędzy właściwości zgodne z wymaganiami zapewniającymi dalszy prawidłowy przerób przędzy na tkaninę. Rokrysol JW20 jest rozpuszczalny w wodzie w każdym stosunku, co zapewnia równomierne naniesienie i pokrycie klejonej przędzy. Po zastosowaniu Rokrysolu JW20 dalsze etapy obróbki tkanin (proces odklejania klejonki, bielenie, barwienie czy drukowanie) zachodzą efektywniej. W przypadku elektryzowania się przędzy w trakcie przerobu zalecane jest dodanie do klejonki specjalistycznego preparatu antyelektrostatycznego Rostat A, który prawie całkowicie eliminuje zjawisko elektryczności statycznej, a także nadaje włóknom dobre właściwości poślizgowe. Produkt sprawdza się w procesach wstępnej preparacji surowców włókienniczych jako dodatek do klejonek przy klejeniu osnów, preparowania surowców po barwieniu oraz finalnego wykańczania tkanin i dzianin.
Kolejnym etapem przekształcania surowca włókienniczego jest dalsza obróbka wstępna. Luźne włókna, przędza, tkanina i dzianina poddawane są bieleniu, barwieniu i uszlachetnieniu. Dobór i kolejność stosowanych operacji jednostkowych uzależniona jest od rodzaju surowca i formy wyrobu (przędza, tkanina lub dzianina).
Przygotowanie wyrobów z włókien bawełny
Obróbka włókien bawełny i innych włókien celulozowych jest bardzo złożona. Wykorzystuje się tutaj głównie takie procesy jak opalanie, odklejanie, merceryzację i bielenie.
Pierwszy proces polega na przeprowadzeniu surowca nad płomieniem palnika gazowego, dzięki czemu usuwane są włókna elementarne.
Kolejnym etapem jest odklejanie, które polega na usunięciu klejonek tkackich. W przypadku klejonek syntetycznych do ich pozbycia wykorzystuje się zazwyczaj pranie w kąpieli wodnej z węglanem sodowym wraz z dodatkami zwilżającymi. Grupa PCC posiada w swojej ofercie szereg środków zwilżających doskonale nadających się do zastosowania w przemyśle tekstylnym. Seria POLIkol (PEG) to grupa polioksyetylenoglikoli, które dzięki swojej budowie wykazują właściwości solubilizujące, zmiękczające, smarne, antyelektrostatyczne oraz nawilżające. Polioksyetylenoglikole charakteryzują się bardzo dobrą biodegradowalnością, a także są bezpiecznymi i nietoksycznymi substancjami, obniżając dzięki temu szkodliwość środowiskową kąpieli wodnych. ROKAnole IT to etoksylowane alkohole tłuszczowe, które zapewniają odpowiednie zwilżenie czyszczonej powierzchni i dyspergowanie cząstek brudu, co wpływa na wysoką jakość usuwania zabrudzeń z tkaniny/dzianiny oraz powierzchni twardych. Produkty te doskonale sprawdzają się jako składniki alkalicznych, a także kwaśnych detergentów stosowanych do profesjonalnego prania i czyszczenia przemysłowego. Z kolei ROKAnole NL znajdują zastosowanie w procesach wstępnej obróbki włókien. Produkty te mogą być wykorzystane do usuwania plam olejowych z tkanin oraz dzianin powstałych w trakcie przemysłowych procesów dziewiarskich i tkackich. ROKAnole NL poprawiają także efektywność bielenia, co bezpośrednio wpływa na poprawę kapilarności barwnika w procesach barwiarskich.
Następnym procesem jest merceryzacja, która ma za zadanie zwiększenie wytrzymałości włókien i zapewnienie im odpowiedniego połysku.
Ostatnim z etapów wstępnego przygotowania włókien bawełny jest tzw. bielenie. Polega ono na odbarwieniu naturalnego koloru wywołanego zanieczyszczeniami na włóknach barwnych (np. w przypadku lnu), których nie można było usunąć na drodze prania. Przykładem takiego związku chemicznego jest chloran (I) sodu, który może być stosowany do wybielania tkanin lnu, konopi oraz dzianin bawełnianych. Dzięki podchlorynowi sodowemu uzyskuje się bardzo wysoki stopień bieli. Aby poprawić efektywność procesu bielenia tuż przed nim stosuje się środki mające na celu neutralizację resztek alkalicznych we włóknach (np. kwas solny).
Obróbka wyrobów wełnianych
Wyroby wełniane również muszą przejść szereg operacji wstępnych przed przeprowadzeniem etapu barwienia. Podstawowymi procesami do ich przygotowania jest karbonizacja, pranie wstępne i bielenie.
Karbonizacja ma na celu całkowite usunięcie zanieczyszczeń roślinnych. Proces ten polega na traktowaniu włókien wełny roztworem kwasu siarkowego, a następnie podgrzaniu ich do temperatury powyżej 100°C. Uszkodzone włókna są mechanicznie usuwane, a całość neutralizowana jest octanem sodu. Po zakończonej karbonizacji następuje etap prania, który ma na celu usunięcie z włókien substancji nanoszonych podczas przędzenia. Dzięki praniu wstępnemu uzyskuje się wysoki stopień zwilżalności oraz chłonności środków bielących i barwników. Ostatnim z etapów jest bielenie wełny, do którego najczęściej jest stosowany nadtlenek wodoru.
Wyroby z włókien chemicznych
Wyroby powstające z włókien syntetycznych także wymagają zastosowania szeregu operacji, wśród których najważniejszymi są pranie wstępnie i stabilizacja termiczna.
Podobnie jak w przypadku włókien naturalnych, pranie wstępne ma za zadania pozbycie się preparacji przędzalniczych z włókien sztucznych. Natomiast stabilizacja termiczna polega na ogrzewaniu w środowisku gorącego powietrza wyrobów, które są transportowane przez kolejne komory grzewcze. Termostabilizacja zapewnia tkaninom stabilność kształtu w finalnych etapach wykończenia, a także podczas użytkowania wyrobów wykonanych z włókien sztucznych.
Barwienie wyrobów włókienniczych
Barwieniu poddaje się wiele wyrobów włókienniczych, takich jak np. luźne włókna, przędza, tkaniny, dzianiny, a nawet wyroby gotowe. Przemysłowo można wyróżnić dwie podstawowe grupy metod barwienia: metody okresowe oraz ciągłe, do których zaliczane są także metody półciągłe.
Metody okresowe polegają na zanurzaniu na określony czas materiału tekstylnego w wodnym roztworze barwnika. Do kąpieli dodawane są także chemiczne środki pomocnicze, które mają za zadanie umożliwiać cząsteczkom barwników migrację do wnętrza włókien. Po zakończeniu takiego procesu kąpiel zostaje odprowadzona do ścieków, a wyrób włókienniczy poddawany jest praniu w celu usunięcia środków chemicznych.
Głównym elementem odróżniającym metody ciągłe od okresowych jest nanoszenie barwnika przez napawanie. Dodatkowo w metodach ciągłych kolejne procesy barwienia przebiegają nieprzerwanie bezpośrednio po sobie, natomiast w metodach półciągłych po napawaniu następuje przerwanie procesu i dalsze etapy są już prowadzone jako operacje niezależne.
Przykładem produktu, który może pełnić funkcję przenośnika we włókiennictwie jest Rokelan OPD. Produkt ten stosowany jest jako przenośnik przy barwieniu włókien hydrofobowych i poliestrowych, zarówno czystych, jak i mieszanych. Pozwala on na uzyskiwanie żywych wybarwień niezależnie od ich koloru oraz intensywności. Wybarwienia przy użyciu Rokelanu OPD wykazują się dobrą odpornością na światło. Ponadto zastosowanie tego produktu gwarantuje wysoką wydajność barwnika.
Chemiczne środki pomocnicze stosowane przy barwieniu
W zależności od rodzajów włókien stosuje się różne dodatki mające na celu usprawnienie procesu barwienia. W przypadku włókien celulozowych, gdzie kąpiele zachodzą w środowisku zasadowym, kluczowym jest utrzymywanie odpowiedniego pH kąpieli. Najczęściej używa się w tym celu ługu sodowego, czyli wodnego roztworu wodorotlenku sodu (sody kaustycznej).
Innymi dodatkami stosowanymi w procesie barwienia włókien celulozowych są środki utleniające (najczęściej stosowany jest tutaj nadtlenek wodoru) i detergenty, które zapewniają skuteczny przebieg operacji prania przeprowadzanej po barwieniu. Seria Roksol (PSWN, ICESOLDE PAN/35L i AZR) to grupa skutecznych środków piorących i czyszczących. Produkty te mogą być stosowane jako środki do przemysłowego prania wyrobów włókienniczych. Bardzo dobrze rozpuszczają się w wodzie i poprawiają efektywność barwienia poprzez swoje właściwości penetrujące. Roksole pozwalają na usuwanie szeregu substancji, takich jak tłuszcze naturalne, natłustki, syntetyczne woski i klejonki. Dzięki swoim właściwościom niskopiennym mogą być używane w wielu procesach technologicznych na różnego typu aparatach, nie powodując zakłóceń w ich pracy.
W przypadku włókien wełnianych, gdzie proces barwienia zachodzi w środowisku kwasowym, w celu zapewniania odpowiedniego pH kąpieli stosuje się kwas siarkowy lub octowy. Dodatkowo do roztworu wprowadzane są także środki redukujące (np. tiosiarczan sodowy) oraz wyrównujące, które mają na celu uzyskiwanie równomiernych wybarwień.
W procesach barwienia włókien syntetycznych także stosuje się szereg dodatków. Włókna PES (poliestrowe) wymagają stosowania zagęstników (np. poliakrylanów) w celu ograniczenia migracji barwnika podczas suszenia. Włókna PA (poliamidowe) wymagają ścisłej kontroli pH i w tym celu używa się kwasu siarkowego lub octowego. Dodatkowo stosuje się także szereg środków wyrównujących i dyspergujących. Grupa PCC w swojej ofercie posiada szereg specjalistycznych produktów mogących pełnić tę funkcję. Dyspergator NNOC E to produkt stosowany w procesach barwienia jako środek dyspergujący i egalizujący. Utrzymuje on trudno rozpuszczalne barwniki w jednorodnej dyspersji w kąpielach barwiących.
Drukowanie wyrobów włókienniczych
Proces drukowania wyrobów włókienniczych polega na miejscowym barwieniu w celu otrzymania ustalonego wzoru. Wszystkie rodzaje włókien wymagają odpowiedniego przygotowania przed drukowaniem. Na substrat włókienniczy nanosi się uprzednio przygotowaną pastę, która zawiera w sobie barwniki lub pigmenty. Następnie tak przygotowane włókna poddaje się procesowi drukowania, który może być wykonywany różnymi metodami (np. druk filmowy płaski, rotacyjny i natryskowy). Po skończonym procesie następuje utrwalanie, inaczej nazywane suszeniem. Końcowym etapem jest pranie, dzięki któremu z włókien usuwane są nieutrwalone cząsteczki barwnika oraz różne środki chemiczne użyte do przygotowania pasty drukarskiej (takie jak dyspergatory lub emulgatory). W tej aplikacji doskonale sprawdzają się etoksylowane nonylofenole, czyli produkty serii ROKAfenol. Ich właściwości detergencyjne, emulgujące i czyszczące sprawiają, że efektywnie wspomagają procesy prania. ROKAfenole mogą być stosowane do czyszczenia różnych włókien, zarówno wełny i bawełny, jak i włókien chemicznych, a także do włosia i skór. Ich odporność na podwyższoną temperaturę i wysokie stężenie elektrolitów powoduje, że mogą być stosowane w trudnych warunkach użytkowania w przemyśle włókienniczym, np. w procesie prania wełny i obgotowywania bawełny.
Wykańczanie tekstyliów
Ostatnim procesem, jakim są poddawane włókna, jest obróbka chemiczna. Jej celem jest nadanie wyrobom określonych właściwości użytkowych np. wodoodporności lub też ograniczenie skłonności do gniecenia. W przypadku zapobiegania gnieceniu się materiałów stosuje się odpowiednie środki sieciujące oraz dodatki zmiękczające.
W procesach wykańczania wyrobów tekstylnych mogą być stosowane takie preparaty jak Roksol AT2 i Roksol AZR. Produkty te sprawiają, że wyroby włókiennicze uzyskują miękki i przyjemny chwyt. Posiadają właściwości zmiękczające i antyelektrostatyczne, dzięki czemu zapobiegają elektryzowaniu się włókien i ułatwiają ich dalszą obróbkę. Roksol AZR posiada również właściwości emulgujące, dzięki czemu wspomaga proces prania i detaszowania. Wyrób charakteryzuje się również dobrymi zdolnościami penetrowania barwnika w kąpieli.
Wykończenia hydrofobowe (wodoodporne) uzyskuje się poprzez dodanie do powierzchni włókien odpowiednich polimerów, które tworzą wodoodporny film. Dodatkowo w celu ich ulepszenia stosuje się także środki silikonowe oraz fluorowęglowe.
Rynek tekstyliów na świecie
Szacunkowa wartość światowego rynku tekstyliów to około 830 mld $ (dane z raportu Grand View Research 2015) i oczekuje się, że liczba ta w najbliższych latach będzie wzrastać. Coraz większa świadomość pracodawców i pracowników dotycząca wyposażenia w środki ochrony osobistej i tym samym zapewnienia bezpieczeństwa podczas pracy jest jednym z ważnych motorów napędowych tego sektora. Ponadto stosowanie coraz nowocześniejszych włókien, takich jak np. kevlar, daje możliwość opracowywania innowacyjnych produktów, które stwarzają nowe możliwości zastosowań na rynku odzieżowym. Kolejnym ważnym aspektem w sektorze tekstylnym jest ciągle obserwowany spadek cen bawełny na niektórych rynkach (szczególnie w Indiach), wynikający głównie z nadprodukcji i wysokiego poziomu zapasów w magazynach.