Kağıt, şu anda bildiğimiz haliyle üretilmeye başlanmasından önce uzun bir yol kat etti. Çin'de icat edildi, en başından beri önemli bir bilgi aracıydı, o zamanlar üretiminde ipek ve keten lifleri kullanılıyordu.
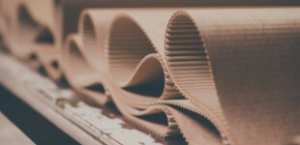
Kağıt yapım süreci
Kağıt üretim süreci birkaç aşamadan oluşur. İlk aşamada, birincil kökenli (odun) veya ikincil (atık kağıt) olabilen hamurun parçalanması ve saflaştırılması gerçekleşir. Selüloz liflerinin ana kaynağı, kereste fabrikalarında çeşitli biçimlerde elde edilen odundur, örneğin kütük, odun yongası veya talaş.
Bir sonraki aşamada, lifli malzeme daha fazla işleme tabi tutulur ve burada hamura dönüştürülür ve daha sonra kağıda işlenir. Hamur üretimi mekanik veya kimyasal yöntemlerle yapılabilir. Kimyasal hamurlaştırma sürecinde, lifleri bağlayan lignini gidermek için genellikle alkali (örneğin, kostik soda veya kostik soda formunda sodyum hidroksit ) kullanılır.
Kağıt üretiminin her aşamasında köpük gidericilerin kullanılması da çok önemlidir. Her türlü kağıt ürününün üretim sürecinde köpük giderici maddeler kullanılır. Köpük, gazların selüloz hamuruyla karıştırılmasıyla oluşturulur ve yüzey aktif maddelerin varlığı nedeniyle içinde tutulur. PCC Group’un sunduğu ürünler, kağıt üretiminin sonraki aşamalarında oluşan köpüğün giderilmesinde başarıyla kullanılabilir. Bunlar arasında EO/PO blok kopolimerleri ( ROKAmer ) ve bir dizi alkoksillenmiş yağ alkolü ( ROKAnol LP ) bulunur. Köpüğün giderilmesinde ve oluşumunun önlenmesinde yüksek etkinlikleri, sonraki teknolojik adımların verimliliğinin iyileştirilmesini sağlar.
Kimyasal hamurlaştırma yöntemleri
Kimyasal hamurlaştırma işlemleri esas olarak lignini yumuşatmak için çeşitli kimyasal reaktiflerin ve ısının kullanılmasından oluşur. Sonuç olarak, çözülür ve daha sonra lifleri ayırmak için mekanik olarak rafine edilir. Uygulamada, iki farklı kimyasal hamurlaştırma işlemi kullanılır.
Bunlardan ilki, sülfat işlemi olarak da bilinen kraft hamurlaştırma işlemidir . Şu anda, baskın teknolojidir – dünya hamur üretiminin yaklaşık %80’i bu yöntem kullanılarak işlenmektedir. Kraft hamurlaştırma, birkaç faktör nedeniyle en yaygın kullanılan yöntem haline gelmiştir. Sülfatla işlenmiş lifler, diğer mevcut teknolojilerin bir sonucu olarak elde edilenlere kıyasla daha iyi dayanıklılığa sahiptir. Ayrıca, her türlü ahşap için kullanılabilir ve işlemin kendisi kullanılan kimyasal hammaddelerin etkili bir şekilde geri kazanılmasını sağlar.
Kraft işlemi, odun yongalarının beyaz likörle ( sodyum hidroksit ve sodyum sülfürün sulu bir çözeltisidir) birleştirilmesinden oluşur. Yüksek basınç ve sıcaklık koşulları altında, bu çözelti lignini çözerek selülozik lifleri serbest bırakır. Sindirim reaksiyonu tamamlandıktan sonra, siyah likör ve selüloz hamuru elde edilir. Sıvı, geri kazanılan ve kimyasal işlemde tekrar kullanılabilen çözünmüş organik maddeler içerir. Lignin, oksijen delignifikasyonu işleminde (oksijen ve sodyum hidroksit varlığında) kütleden uzaklaştırılır. Bu şekilde elde edilen malzeme, nihai ürünün mukavemeti, parlaklığı ve saflığı gibi uygun performansa ulaşmak için ağartılır.
Kimyasal sindirimin ikinci işlemi sülfit işlemidir . Alkalilerin (örneğin kalsiyum, magnezyum, sodyum ve amonyum) varlığında sulu bir kükürt dioksit çözeltisinin kullanılmasından oluşur. Bu işlemde elde edilen ürünler daha hafiftir ve beyazlatılması daha kolaydır, ancak daha sık kullanılan sülfat hamurlaştırmaya kıyasla çok daha düşük mukavemete sahiptirler. Sülfit işlemi ayrıca odun hammaddesinin dikkatli seçilmesini gerektirir – bu yöntem örneğin çam ağacı için toleranssızdır. Kraft hamurlaştırmaya kıyasla sülfit işlemi daha verimlidir, daha az hoş olmayan gaz üretir ve ayrıca kolayca yıkanan çok hafif bir hamur elde edilmesini sağlar. Ne yazık ki, elyaf kalitesinin düşük olması, enerji tüketiminin fazla olması ve proseste kullanılan kimyasal hammaddelerin geri kazanılabilirliğinin düşük olması nedeniyle sülfit teknolojisi yerini kraft prosesine bırakmıştır.
Mekanik hamurlaştırma yöntemleri
Mekanik hamurlaştırma, odun hamurundan çok yüksek verim sağlar. Endüstriyel ölçekte kullanılan ana işlemler, taş öğütülmüş odun hamuru (SGW), termomekanik hamurlaştırma (TMP) ve kemo termomekanik hamurlaştırma (CTMP) işlemidir.
Öğütülmüş odun hamuru, odunun taş üzerinde atmosferik basınçta aşındırılması işlemiyle elde edilir. (Daha önce kabuğu çıkarılmış olan) odun, taş kullanılarak hamur haline getirilir ve daha sonra suyla yıkanır. Hazırlanan kütle, sıkıştırıcıya taşındığı hidrosiklonlarda kurutulur. Bir sonraki aşamada, yoğun odun kütlesi tekneye taşınır ve dolaşan su (filtrat) hamur değirmenine geri dönüştürülür. İşlenmiş odundan hamur üretimi sırasında, kolayca aglomere olan ve öğütücüde veya boru hatlarının iç duvarlarında tortu oluşturan reçineli maddeler açığa çıkar. Bunlar genellikle taşın yüzeyinin kirlenmesine neden olur ve bu da aşındırıcı özelliklerini kötüleştirir. Bu sözde "reçine sorunlarını" gidermek için çeşitli kimyasal maddeler kullanılır. Bu amaçla en yaygın kullanılan madde, oluşan tortuları dağıtmak ve daha sonra bunların çıkarılmasını kolaylaştırmak için tasarlanmış dağıtıcılardır. ROKAcet ve ROKAfenol serisinin ürünleri, kağıt hamuru ve kağıt endüstrisine adanmış mükemmel dağıtıcılardır. Bu ürünler, dağıtma kabiliyetlerine ek olarak, temizlik maddesi, emülgatör ve anti-elektrostatik madde olarak da işlev görebilir. ROKAfenoller, kağıt hamuru ve selülozun emülsifikasyon ve leke çıkarma işlemleri için mükemmeldir. ROKAcet R40W ise tekstil, deri ve kağıt endüstrisinde kullanılabilen yumuşatıcı özelliğe sahip bir üründür.
SGW yönteminin iyileştirilmesi termomekanik hamurlaştırmadır (TMP). TMP işleminde, odun yongaları başlangıçta kum, taş ve diğer sert kirleticileri gidermek için yıkanır, ardından artan basınç altında buharla ısıtılır ve daha sonra bir disk değirmeninde hamurlaştırılır. Bir sonraki aşamada, kütle, liflerin düzeltilmesi ve deformasyonunun ortadan kaldırılmasının gerçekleştiği tekneye taşınır. Son olarak, depolama tankına yönlendirilir. TMP işleminde oluşan zararlı reçinelerin miktarını azaltmak için, SGW işleminde olduğu gibi benzer kimyasallar kullanılır. Bu şekilde oluşturulan kütle çoğunlukla gazete kağıdı üretimi için kullanılır.
CTMP işlemi, TMP işlemini yongaların kimyasal emdirilmesiyle birleştirir. İlk aşamada yıkanır, elenir ve ardından emdirilir. Odun türüne bağlı olarak uygun kimyasal çözeltiler kullanılır. Yumuşak ağaçlar için genellikle sodyum sülfat kullanılırken, sert ağaçlar için genellikle alkali peroksitler seçilir. Emprenye işlemi tamamlandıktan sonra yongalar ısıtılır ve su ile karıştırılır, bu da lignin bağlarını gevşetir ve lifleri serbest bırakır. CTMP işlemi, yeterli mukavemete ve uygun optik özelliklere sahip temiz hamur elde edilmesini sağlar. CTMP, esas olarak baskı ve hijyen kağıtlarının üretiminde kullanılabilen kağıt hamurunun lifli bileşenlerinin üretiminde kullanılır.
Flotasyon ve ağartma
Hamur işlemenin bir sonraki aşaması, kirliliklerin mekanik olarak giderilmesiyle birleştirilmiş mürekkep gidermedir. Kağıt üretiminde en önemli parametre renktir (beyazlık – baskı kağıdı durumunda). Bu nedenle, geri dönüştürülmüş kağıt baskı mürekkebinden iyice temizlenmelidir. Giderilmesinin temel koşulu, boya parçacıklarının liflerden ayrılması ve bunların dağılmış bir durumda tutulmasıdır. İnce bölünmüş mürekkep parçacıkları daha sonra lif süspansiyonundan ayrılır. Bu genellikle, istenmeyen maddelerin liflere ve suya kıyasla özgül ağırlığı gibi malzemelerin fiziksel özelliklerindeki farklılıklar temelinde yapılır. Metal parçalar (zımba telleri), taşlar ve kum gibi daha büyük kirliliklerin lif giderme aşamasında zaten giderilmiş olması nedeniyle, ince kirliliklerle ilgili olarak flotasyon işlemleri çok sık kullanılır.
Sık kullanılan ek bir işlem ağartmadır ve sararmanın istenmediği yüksek saflık gerektiren ürünlerde kullanılır (örneğin yazma ve baskı kağıtları). Sodyum hipoklorit , ağartma için kullanılan çok popüler bir maddedir. Ayrıca talaştan karboksimetil selüloz (CMC) üretimi için de kullanılabilir. Bu işlemde sodyum hidroksit çözeltisi vekloroasetik asit (MCAA) de kullanılır. Ağartma, kütlenin beyazlığını artırmak için doğrudan dağıtıcıya eklenen uygun kimyasalların kullanımını içerir. Kullanılan elyaf türü ve ürünün istenen son özellikleri, hamur ağartma derecesi üzerinde büyük bir etkiye sahiptir. Yüksek yoğunluklu malzemeler içeren kütlelerin ağartılması zordur ve yüksek dozda kimyasal gerektirir. Ağartma tesislerinden geri dönüştürülmeden önce çıkan kanalizasyon, köpürmesini, aşındırıcılığını veya kireç oluşturma yeteneğini azaltmayı amaçlayan bir dizi kimyasal madde gerektirir. PCC Group’un ROKAmers gibi ürünleri, kanalizasyon ve teknolojik suların köpürmesinin meydana geldiği işlemlerde kullanım için mükemmeldir. ROKAmer ürünleri etilen oksit ve propilenin blok kopolimerleridir. Bu ürünler sıvı ile hava arasındaki yüzey gerilimini azaltırken aynı zamanda köpüğün "drenajını" iyileştirerek aslında azalmasına neden olur.
Kağıt hamurunun son işlenmesi
Çözünme, flotasyon ve ağartma işlemlerinden sonra, bitmiş selüloz hamuru kağıt hamuruna işlenir ve daha sonra kağıt üretimi için kullanılır. Bu işlem birkaç aşamayı içerir:
- selüloz hamurunun karıştırılması,
- Suda hamur dispersiyonunun oluşumu,
- rafine etme,
- gerekli ilavelerin yapılması.
Katkı maddeleri, özel özelliklere sahip kağıt ürünleri (özel kağıtlar olarak adlandırılır) üretmek veya kağıt sürecini iyileştirmek için kullanılır. En popüler katkı maddeleri şunlardır:
- hidrofobikleştirme için reçineler ve mumlar,
- örneğin kil, talk ve silika gibi dolgu maddeleri,
- inorganik ve organik boyalar,
- baskının yapısını, yoğunluğunu, parlaklığını ve kalitesini iyileştiren inorganik bileşikler (örneğin titanyum dioksit, kalsiyum sülfat ve çinko sülfür),
- e) emülgatörler ve temizlik maddeleri. PCC Group, her iki işlevi de yerine getirebilen ROKAcet ürün serisini sunmaktadır. Yapıları sayesinde, kağıt endüstrisinde düşük köpüren ve yumuşatıcı maddeler olarak da kullanılabilirler.
Son aşamada, kütle özel makineler kullanılarak bir kağıt ürününe işlenir. İşlem tamamlandıktan sonra, kağıt hasardan ve kirden korunmak için rulo haline getirilir. PE-kağıt laminat, kağıdın paketlenmesinde en yaygın kullanılanıdır. Bu tür paketleme, mekanik hasara, toza ve neme karşı iyi koruma sağlar. Bu tür paketlemenin en büyük avantajı da tamamen geri dönüştürülebilir olmasıdır.